Strong Bone Cement Produced in Iran for Orthopedic, Trauma Surgeries
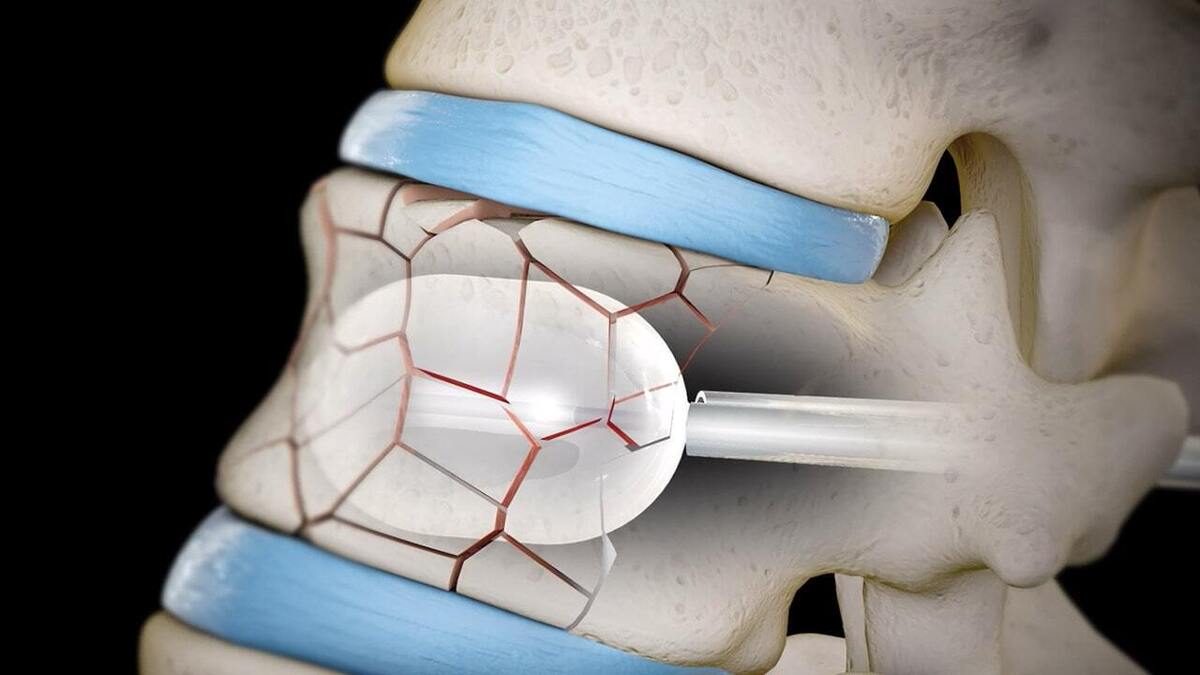
“Bone cement is widely used to connect defective and fractured bones, fill holes caused by bone tumors and keep implants stable in orthopedic and trauma surgeries,” said Mohsen Shahrousavand, an assistant professor of Caspian technical faculty of University of Tehran and one of the researchers of the project.
“For instance, vertebroplasty and kyphoplasty are two types of surgery that surgeons perform to treat spine fractures caused by osteoporosis and vertebral fractures, and bone cement is used in these operations,” he added.
Noting that cements based on polypropylene femurate (PPF), calcium phosphate bone cements (CPBCs), glass ionomer cements (GIC), acrylic cements or cements based on polymethyl methacrylate (PMMA) exist in the market, Shahrousavand said, “Polymethyl methacrylate cements are generally two-component materials and consist of methyl methacrylate polymer powder and methyl methacrylate monomer liquid. Since the cements used in orthopedic applications need to withstand physical forces, therefore they should have appropriate compressive strength.”
Elaborating on advantages of the Iran-made bone cements, he said, “To control temperature during setting, calcium phosphate nanoparticles derived from oyster shell powder were used, and cellulose nanoparticles modified with calcium phosphate increased the mechanical strength of bone cement. At the same time, these materials have led to the improvement of the bioactive properties of bone cement, which has greatly reduced the inflammatory reactions in the body.”
“In this project we used zinc oxide nanoparticles to increase the antibacterial properties of the bone cement,” Shahrousavand said.
In a relevant development late last year, a group of Iranian researchers from Sharif University of Technology had also succeeded in developing a platform for designing and manufacturing customized titanium implants to replace bone.
“The remarkable thing about custom implant production is that each product is designed and manufactured specifically and based on the specifications of any patient, and therefore it is different from other products,” said Farzam Farahmand, a faculty member of the Mechanical Engineering Department of Sharif University of Technology.
He added that unlike the common mode of industrial production in which the product is standardized, in customized production, the product cannot be standardized, but the production process chain must be standardized.
“In this project, all stages of designing, manufacturing and finishing operations of customized titanium implants have been studied, modeled, analyzed and tested,” Farahmand said, adding that the production process chain includes conceptual and detailed design, manufacturing based on the SLM method, completion of surface and thermal operations and final processing like washing and sterilization, and all these stages have been optimized, standardized and documented.
“Customized bone replacement implants have wide applications in various types of surgery, specially maxillofacial surgery and orthopedic surgery. The platform developed in this project is capable of designing and production of different types of these implants, including articular and non-articular implants, cemented and non-cemented implants (direct connection of implant and bone), solid and porous implants, and implants bearing small, medium (such as bite force) and large mechanical loads (such as weight force) optimally and standardly,” he underlined.
4155/v