Scientists Use Cutting Edge Thermoplastic Materials in Aerospace Sector
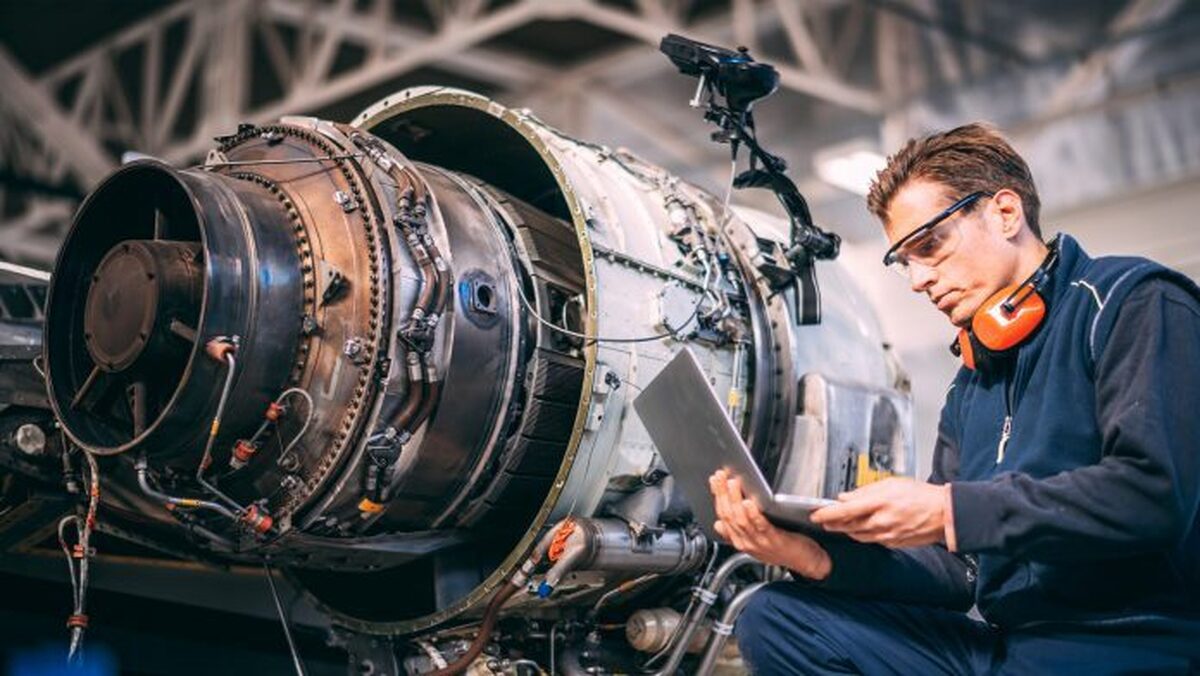
The HITCOMP (High Temperature Characterisation and Modelling of Thermoplastic Composites) project, which is part of the Horizon 2020 programme, aims to study the potential advantages of utilising thermoplastic materials in the aerospace industry. The Universidad Carlos III de Madrid (UC3M) has coordinated this project, the Innovation News Network reported.
The European aerospace sector typically uses low-weight, high-performance thermosetting plastic composites—also known as epoxy resin-based composites—in many of their applications. However, these materials are not as efficiently heat resistant as other metal aircraft components.
This can compromise safety in situations where extreme temperatures are achieved. In an effort to improve the current thermosetting composites’ behaviour in the face of heat destruction, the HITCOMP research team has proposed an alternative: the use of new PAEK resins-based thermoplastic materials.
During the development of the HITCOMP project, components created from a thermoplastic base have demonstrated higher efficiency – due to their thermal properties – than thermosetting composites. They are very useful due to their ability to be recast, reshaped, processed, and recycled, without the need for any additional curing process in order to harden and set.
In addition, they are more versatile, cheaper, and eco-friendly materials than conventional thermosetting composites. They also have a longer service life as due to their high resilience they can be recycled or repaired more easily and survive effects of fatigue resistance, wear and tear, and corrosion. The introduction of these materials would mean having safer and lighter aircrafts which consume less fuel, improve energy efficiency, and reduce their emissions.
To receive the most out of thermoplastics potential in the aerospace industry, it is necessary to determine their behaviour when subjected to heat, fire, and mechanical loads, due to their capacity to melt and deform when overheated.
The HITCOMP project has developed a test laboratory with new infrared (IR) thermography techniques in order to obtain accurate and non-intrusive measurements of the specific temperature of materials during fire tests. The fundamental aim is to conduct virtual tests on thermoplastics and compare their performance in real applications with those of conventional thermosetting composites.
“The aerospace sector is undergoing a transition to a more electric aircraft,” explained Fernando López, lead researcher and coordinator of the HITCOMP project, from the UC3M Department of Physics. “This involves more heat and eventually fire sources, increasing the heating effect on the structure. In this context, our project aims to establish an innovative methodology which allows a characterisation of thermoplastics that involves fewer resources and improves the prediction of their behaviour and resistance when subjected to mechanical loads or fire and high temperatures.”
The measurements obtained by infrared thermography allow computer simulations to be carried out, which virtualise testing to select this type of material in the aeronautical industry. The IR models and equipment have already been transferred to the Airbus company so that they can study their industrial application.
During the research process, the team has also developed a novel method — inspired by the previous results of UC3M’s Sensors, Remote Detection and Infrared Imaging Laboratory (LIR-InfraRed LAB)— which allows the use of these infrared imaging techniques to remotely determine the thermal properties of these materials, without contact.
4155/v