Knowledge-Based Company Supplies 65% of Iran’s Need to Titanium Implants
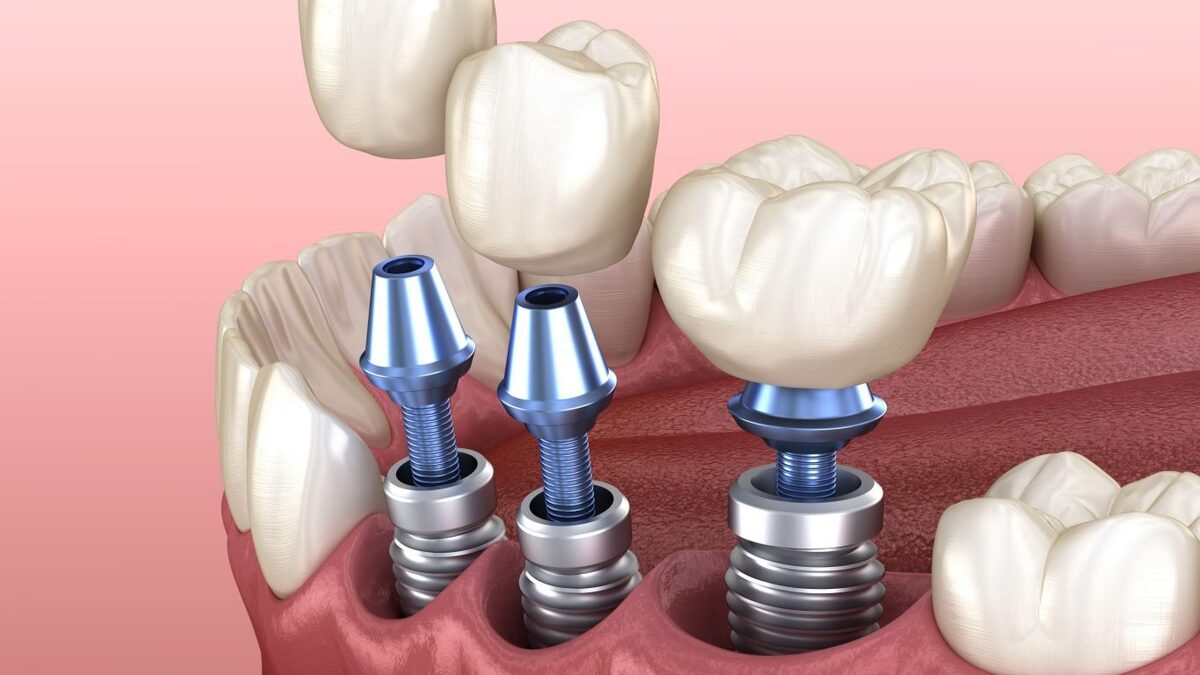
“The products made by our company are manufactured by using the best raw materials available in the world market under the supervision of the Iranian health ministry and are made with high quality and this product is not only competitive with foreign products, but is also sold at half the price of European and US products and they are supplied to the academic and medical centers in Iran,” said Khosro Mohammadlou, the managing director of the knowledge-based company.
He noted that the company currently supplies 65% of the jaw and face implants and 10% of the spine implants to the Iranian market.
“We also export about 15% to 20% of our products to Germany. Our parts enjoy international standards based on which we are now in the process of receiving the European CE to be able to export our products directly from Iran to all countries,” Mohammadlou said.
In a relevant development, a group of researchers from Sharif University of Technology had also succeeded in developing a platform for designing and manufacturing customized titanium implants to replace bone.
“The remarkable thing about custom implant production is that each product is designed and manufactured specifically and based on the specifications of any patient, and therefore it is different from other products,” said Farzam Farahmand, a faculty member of the Mechanical Engineering Department of Sharif University of Technology.
He added that unlike the common mode of industrial production in which the product is standardized, in customized production, the product cannot be standardized, but the production process chain must be standardized.
“In this project, all stages of designing, manufacturing and finishing operations of customized titanium implants have been studied, modeled, analyzed and tested,” Farahmand said, adding that the production process chain includes conceptual and detailed design, manufacturing based on the SLM method, completion of surface and thermal operations and final processing like washing and sterilization, and all these stages have been optimized, standardized and documented.
“Customized bone replacement implants have wide applications in various types of surgery, specially maxillofacial surgery and orthopedic surgery. The platform developed in this project is capable of designing and production of different types of these implants, including articular and non-articular implants, cemented and non-cemented implants (direct connection of implant and bone), solid and porous implants, and implants bearing small, medium (such as bite force) and large mechanical loads (such as weight force) optimally and standardly,” he underlined.
4155/v