
ورق استیل آهنی (Ferritic)
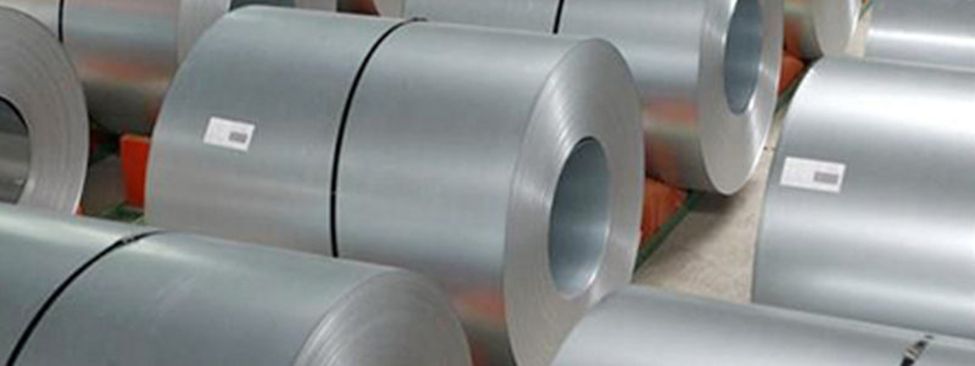
به گزارش گروه بازار خبرگزاری آنا، ورق استیل آهنی دارای یک ریزساختار فریتی مانند فولاد کربنی می باشد که یک ساختار کریستالی مکعبی مرکز-بدنی (body-centered cubic) محسوب میشود. این فولا ضد زنگ دارای ۱۰٫۵ تا ۲۷ درصد کروم و مقدار بسیار کمی نیکل یا بدون نیکل می باشد. این ریزساختار به علت اضافه شدن کروم، در همه درجه حرارتها وجود دارد و مانند ورق پرفروش استیل آستنیتی با عملیات حرارتی سختکاری نمیگردد. مانند ورق استیل آستنیتی آنها را نیز با کار سرد نمیتوان تقویت نمود. این فولادها مانند فولاد کربنی مغناطیسی می باشند.
فولادهای ضد زنگ فریتی معمولاً خود به ۴ گروه طبقهبندی میشوند:
- گروه ۱ که دارای ۱۰ تا ۱۴ درصد کروم و عدد معادل مقاومت به حفره دار شدن حدود ۱۰ است، در شرایط غیر سخت یا زمانی که مقداری خوردگی سطحی قابل قبول است استفاده میشود. گریدهای معمول (EN 1.4003) AISI 403 و AISI 409Cb (EN A/4601) می باشد که در لولههای اگزوز خودروها استفاده میشود.
- گروه ۲ که دارای ۱۴ تا ۱۸ درصد کروم و با عدد معادل مقاومت به حفره دار شدن حدود ۱۶ است. معروفترین گرید آن AISI 430 (EN 1.4017) است. این گرید برای جوشکاری مناسب نمی باشد، زیرا رشد دانه در منطقه آسیب دیده حرارتی جوش موجب شکنندگی می گردد.
- گروه ۳ بسیار شبیه به گروه ۲ است، اما افزودن Nb نیوبیوم، تیتانیوم Ti و زیرکونیم Zr در مقادیر کم، تهنشینی کاربید را افزایش خواهد داد که به نوبه خود سبب جلوگیری از رشد دانهها و شکنندگی جوشها می گردد؛ بنابراین بدون هیچ مشکل خاصی قابل جوشکاری می باشند.
- گروه ۴ گریدهای این گروه را میتوان «فوق آهنی» بگوییم که دارای مقادیر بیشتری Mo مولیبدن، وکروم Cr میباشد.( عدد PREN) عدد معادل مقاومت به حفره دار شدن آنها بالای ۱۸ است، که این نوع را برابر یا بهتر از (EN 1.4301) AISI 304 میکند. شناخته شدهترین گرید این خانواده AISI 434 و ۴۴۴ به ترتیب EN 1.4113 و EN 1.4521 می باشد.
گریدهای با مقاومت الکتریکی بالا Fri-Cr-Al شامل این گروهها نمیباشد، زیرا آنها را برای مقاومت دربرابر اکسید شدن در دمای بالا طراحی شده اند.
ورق استیل آهنی
متالوژی ورق استیل
به نقل از سایت فروش استیل خانی در متالورژی، فولاد زنگنزن یا فولاد ضدزنگ یا ورق استیل استنلس ، آلیاژی از فولاد است. اصلیترین عناصر تشکیلدهنده آن آهن، کروم و نیکل می باشد. حداقل درصد جرمی کروم در آن ۱۰٫۵ درصد و حداکثر درصد جرمی کربن آن ۱٫۲ درصد می باشد. فولادهای ضد زنگ به دلیل ویژگی غیرفعال شدن خود میتوانند مقاومت بسیار خوبی دربرابر خوردگی از خود بروز دهند. این فولادها به دلیل شکل گرفتن یک لایه غیرفعال که بر روی سطحشان تشکیل می شود در برابر خوردگی مقاوم می شوند. این لایه به شدت با ماده زیرین پیوند می دهد و از تماس بیشتر ماده با محیط اطراف جلوگیری مینماید. برای اینکه این پدیده غیرفعالسازی بهطور پایدار در فولاد اتفاق بیفتد نیاز می باشد که حداقل ۱۰٫۵ درصد از ماده را کروم تشکیل بدهد.. باوجود چنین سطحی از کروم حتی اگر خراشی بر روی سطح فولاد ایجاد گردد. در صورتیکه این لایه از بین برود فولاد میتواند خودش را ترمیم نماید. اگر گرید به درستی برای محیط کاری انتخاب شود. این لایه غیرفعال دوباره تشکیل می گردد. در غیراینصورت شکست غیرفعالی رخ خواهد داد و ورق استیل زنگزده و خورده میشود. ورق استیل به خاطر مقاومت دربرابر خوردگی خود بسیار مورد توجه هستند که این ویژگی با افزایش میزان کروم افزایش مییابد. افزودن عنصر مولیبدن باعث افزایش مقاومت به خوردگی فولادهای ضد زنگ فریتی در مقابل اسیدهای کاهنده و دربرابر خوردگی در محلولهای کلرایدی میگردد. به همین دلیل، انواع مختلفی از فولاد ضد زنگ با میزان مختلف کروم و مولیبدن برای مطابقت با محیطی که آلیاژ باید تحمل کند تولید می شود. ورق استیل به شکل ورق، صفحه، میله، سیم و لوله تولید میشود. مقاومت خوب در برابر خوردگی، راحتی در تمیز نمودن و استریل نمودن با بخار و عدم نیاز به پوشش دادن سطحی،از ویژگی های آن می باشد. این ویژگی ها استفاده از ورق استیل را در آشپزخانههای تجاری و صنعتی متداول نموده است.
ورق استیل آهنی
نقش عناصر آلیاژی مختلف
- کروم: نقش کروم بیشتر در دماهای بالای ۵۰۰ درجه سلسیوس بروز می کند. این عنصر باعث شکل گرفتن یک لایه اکسید غنی از کروم مقاوم بر روی سطح شده که از رسیدن بیشتر اکسیژن به لایههای زیرین و در نتیجه زنگزدگی محافظت می نماید.
- سیلیکون و آلومینیوم: نقش سیلیکون و آلومینیوم مشابه نقش کروم می باشد. اگر این عناصر به اندازه کافی در سطح موجودداشته باشند میتوانند باعث شکل گرفتن لایههای SiO2 اکسیدسیلیکون و Al2O3 اکسید آلومینیوم در سطح گردند. برای شکل گرفتن بیشتر این لایهها مقدار کمی از عناصر فلزی کمیاب مانند سریم یا لانتانوم میتواند بسیار مفید باشند.
- نیکل: نیکل باعث افزایش چقرمگی، استحکام دمابالا و افزایش مقاومت در مقابل کربونیزه شدن و نیتریده شدن گردد.
- نیتروژن و کربن: باعث افزایش استحکام خزش میگردند.
- مولیبدن: باعث افزایش استحکام ترکیدگی ناشی از خزش خواهند شد.
- تیتانیوم: درصد کمی تیتانیوم، در حدود ۰٫۳ تا ۰٫۷ درصد، میتواند در فولادهای آستنیتی باعث افزایش استحکام گردد.
- بور: بور در غلظتهای بسیار پایین، در حدود ۰٫۰۰۲ درصد باعث افزایش استحکام ترکیدگی ناشی از خزش می گردد.
انتهای پیام / ر
انتهای پیام/