Scientists Develop Technology for Sustainable Production of Industrial Chemicals
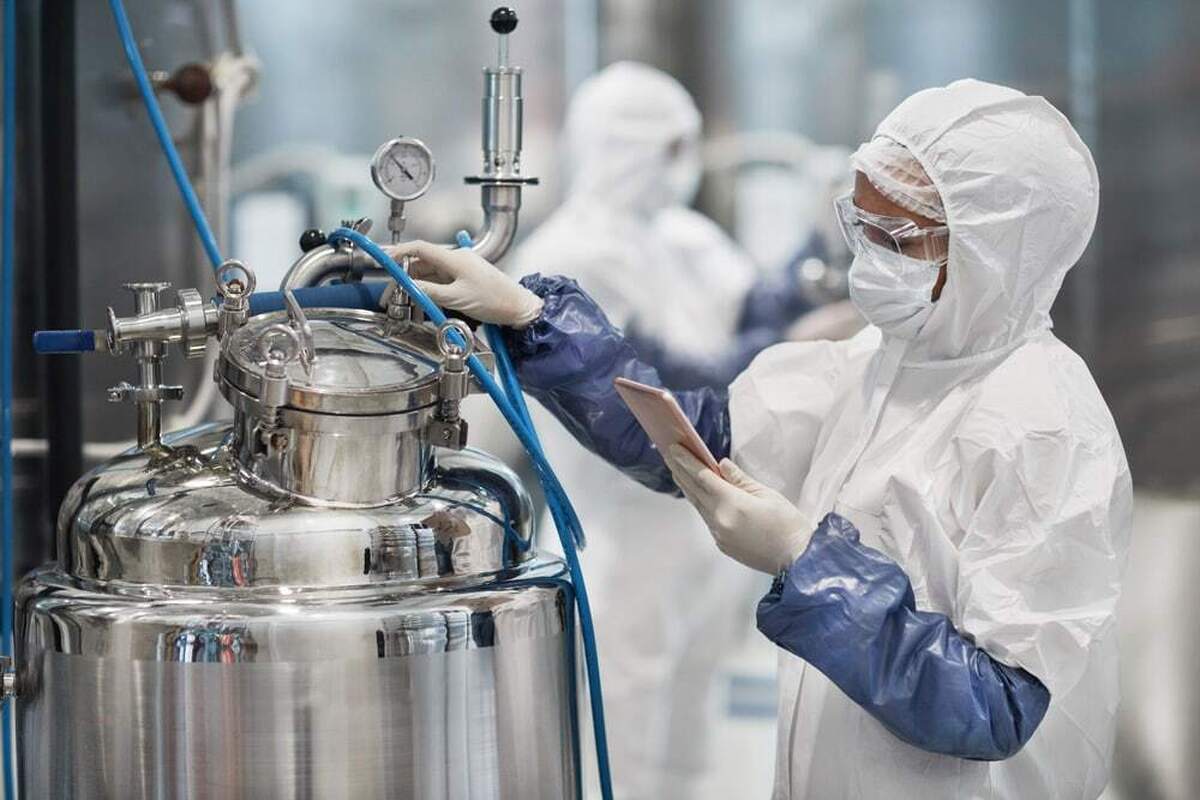
This breakthrough will also support China's sustainable economic development and the realization of the nation's "dual carbon" goal, which refers to peaking its carbon dioxide emissions by 2030 and achieving carbon neutrality by 2060, according to Zheng Mingyuan, a researcher with the Dalian Institute of Chemical Physics (DICP) of the Chinese Academy of Sciences.
A research team from DICP and SinoSci Bio-EG (Zhengzhou) New Energy Technology Co., Ltd. successfully completed pilot testing of the biomass-to-bio-EG catalytic conversion technology at a scale of 1,000 tonnes annually, which passed evaluation by the China Petroleum and Chemical Industry Federation.
EG, mainly used in the synthesis of polyester fibers, polyester bottles, antifreeze, coatings and pharmaceuticals, has an annual global consumption of over 30 million tonnes. China is a major producer and consumer of EG, with an annual consumption exceeding 20 million tonnes.
However, EG is primarily produced from petroleum or coal, which has disadvantages such as reliance on non-renewable resources, high carbon dioxide emissions, and high energy consumption. Therefore, the development of green and efficient EG production technologies is urgently needed, Zheng noted.
In 2008, the research team led by Zhang Tao, an academician at the CAS, pioneered the direct catalytic conversion of cellulose into EG at DICP, establishing a novel pathway for producing bio-based EG.
In the subsequent years, the team conducted systematic research focusing on fundamental understanding and industrial applications. They achieved significant progress in developing low-cost catalysts, investigating reaction mechanisms, converting raw materials and creating high-efficiency reaction systems.
In 2022, the team of researchers, in collaboration with SinoSci Bio-EG and other partners, built the world's first pilot facility for 1,000-tonne bio-EG production through catalysis in Puyang in central China's Henan Province. The team later carried out technological improvements for the project.
Zheng explained that the pilot facility employs the biomass feedstock of sugars derived from starch and corn stalks to produce EG through a highly selective catalytic reaction system, combined with an efficient product separation process. The entire process follows a green, low-carbon route.
With over 40 authorized invention patents, this technology boasts a comprehensive portfolio of independent intellectual property rights, according to Zheng.
The pilot operation has laid the foundation for the industrial application of the technology at a scale of 10,000 tonnes annually, Zheng said.
4155/v