Young Iranian Researcher Produces Machine to Make Hemostasis Valves
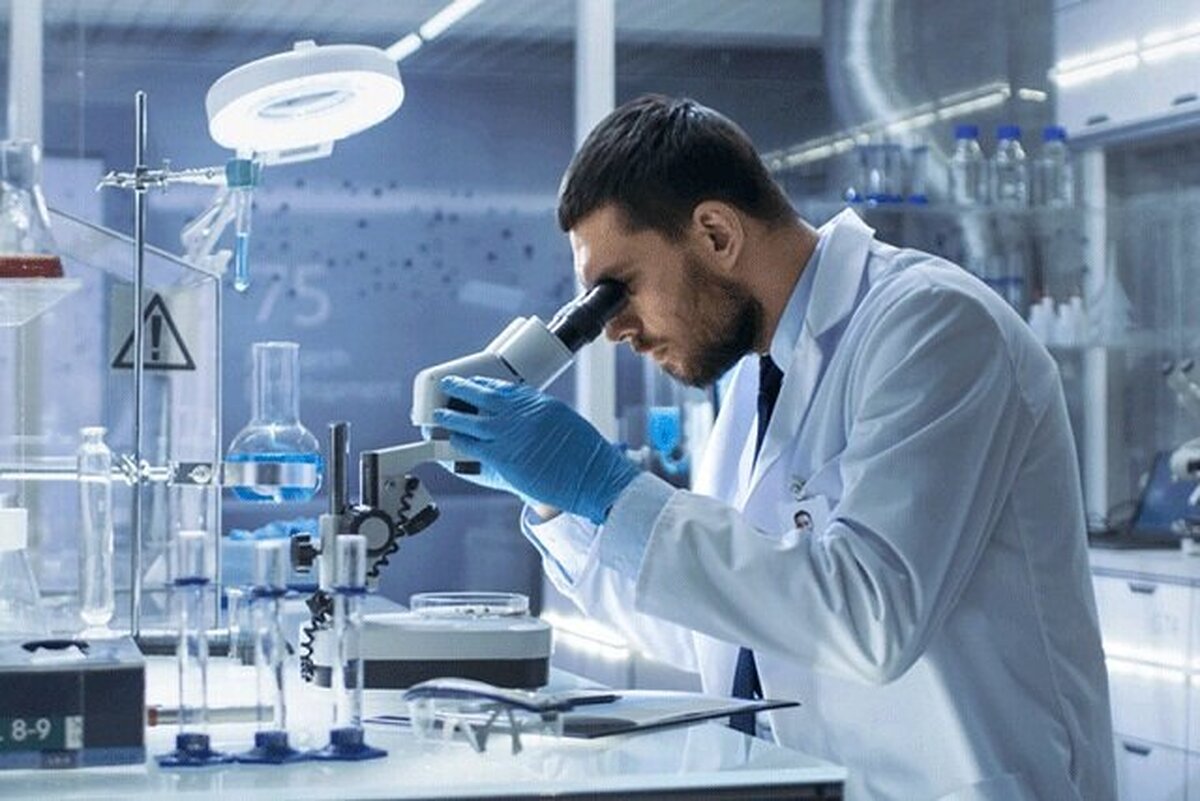
Sponsored by Iran's Biotechnology Development Headquarters, Abdul Rahman Haqiqi was a researcher who carried out the research that led to the production of a machine to make hemostasis valves in large numbers, a report by the Vice-Presidency for Science and Technology and Knowledge-Based Economy said.
The domestically-made machine allows for the production of vital parts in angiography drapes and was designed and built in one of the knowledge-based companies. It lays the ground for the country's self-sufficiency in producing that regard by relying on domestic capabilities, the report added.
In the first phase of this project, firstly, the material and design of the valves available in the domestic and global markets were assessed. After that, by consulting specialists, as well as studying the international registered patents and reports, the most important challenges were known, as well as the optimal design and material of the valve. At this stage, it was decided to produce a silicone valve with a cross slit design. The design of the device was centered around achieving that goal.
According to the Vice-Presidency's report, in the next phases of the research project, the parts of the sampling mold, silicone injection kit (pad), cutting mechanism and control unit were designed and made and the necessary optimizations were followed. For example, in the part of the sampling mold, by optimizing the depth of the holes, the geometry of the air outlet, polishing the surface, etc., defects such as the turbidity (being blur) of the part and the presence of bubbles in it were reduced to the minimum possible. Then, the silicone injection kit was designed, focusing on the pressure injection of liquid silicone, from two components of the same volume, A and B, and then a creative and innovative cutting mechanism was designed and built to create a cut with the desired characteristics on the molded silicone piece. Finally, a control unit was designed to control the operation of the machine to complete it.
"One of the most important challenges in this direction is the necessity of placing the machine in a clean room and the need to meet its requirements, including the ability to sterilize it, the possibility of opening it on site for cleaning and repair operations, and also not creating tiny particles when it is operating," the report added.
Despite all the challenges, the device built as a result of the project has successfully passed all the necessary tests and meets all the validation requirements, the report concluded.
4155/i