Iran Breaks Monopoly of Production of Large Copper Casting Wheels
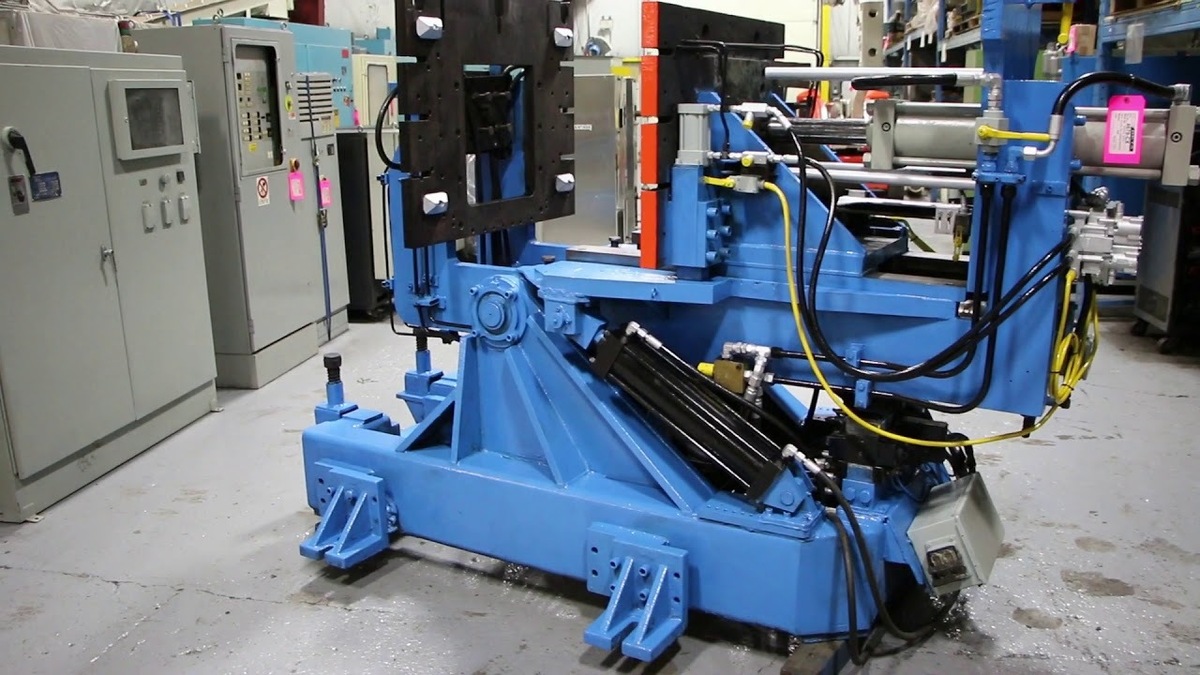
“The research and technology center for processing special metal materials of the Academic Center for Education, Culture and Research of Tehran was able to make the casting wheel by obtaining technical know-how and all necessary approvals,” said Nader Al-e Ebrahim, the supervisor of the research and technology center for processing special metal materials of the Academic Center for Education, Culture and Research of Tehran.
Noting that the two German companies of KME and the French Lebronze had managed to register the copper-chromium-zirconium alloys used in the form of copper crystallizer under the names ELBRODUR and CRM16E respectively, in their name, he said, “The Iranian researchers succeeded in producing a large copper casting wheel for continuous metal casting and broke this monopoly.”
“This center has acquired the technical know-how to make all the master alloys needed to make this product, which was previously imported, so not only the process of making the large copper casting wheel for continuous metal casting, but also all its raw materials are made in this center. Copper-chromium-zirconium alloy is a composite material that is used to make copper casting wheel parts,” Al-e Ebrahim said.
“This alloy is a combination of copper, chromium and zirconium and has unique features like resistance to oxidation,” he added.
The casting machine consists of pouring ladle, constant volume casting ladle with balancing device, casting wheel, water spraying device, anode lifting pin , mold dressing spraying device, defective anode rejection device and anode copper water cooling tank, etc.
The casting ladle has a balancing system to control the pouring ladle so that the precise amount of copper can be put in. The casting ladle tilts to discharge all the content to casting molds. On the casting wheel, casting molds are supported, usually 4-18 molds depending on the capacity, maximum 100t/h with two casting wheels.
The casting wheel is driven by serve motor and revolution structure to maintain smooth and stable rotation for high casting quality. The “backward sliding” movement of casting ladle changes the pouring point continuously from anode feet to ear, resulting in uniform molten distribution and longer service lifetime of mold and avoiding overflow of copper liquid at the mold feet.
The mold is heated prior to casting anodes. An additional purging system is used to clean the mold free from water and impurities. A lifting pin is designed to elevate the anode prior to removal.
4155/v