New Polymers Made from Plant Cellulose
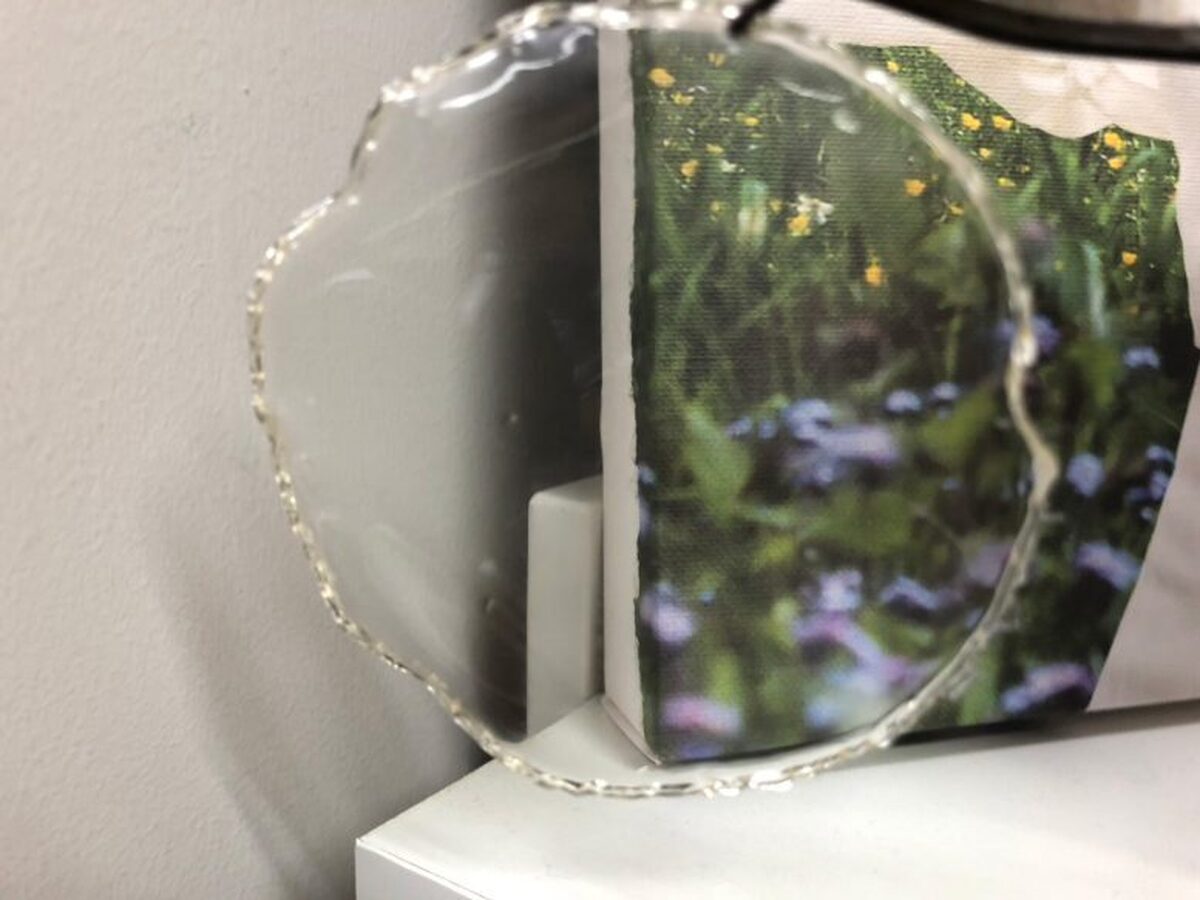
This is a key requirement to reduce the burden of plastic pollution in the environment. They developed a convenient and versatile method to make a variety of polymers from chemicals derived from plant cellulose; crucially, these polymers can be fully recycled. The method was published in the journal ACS Macro Letters.
Cellulose is one of the most abundant components of biomass derived from plants, being a key part of the tough cell walls surrounding all plant cells. It can be readily obtained from plant wastes, such as straw and sawdust, therefore, using it as a feedstock for polymer manufacture should not reduce the availability of agricultural land for food production. Cellulose is a long-chain polysaccharide polymer, meaning that it is composed of multiple sugar groups, specifically glucose, linked together by chemical bonds.
To make their new polymers, the Hokkaido team used two commercially available small molecules, levoglucosenone (LGO) and dihydrolevoglucosenone (Cyrene), which are made from cellulose. They developed novel chemical processes to convert LGO and Cyrene into a variety of unnatural polysaccharide polymers. Varying the precise chemical structure of the polymers offers the ability to generate different materials for a range of possible applications.
“Our biggest challenges were controlling the polymerization reaction that links the smaller monomer molecules together, and obtaining polysaccharides materials that are sufficiently stable for common applications while still able to be broken up and recycled by specific chemical conditions,” says Assistant Professor Feng Li, a corresponding author.
Li adds that the biggest surprise during the research was the high transparency of the polymer films they made, which might be crucial for the kind of specialist applications that these polymers seem most suited for. “As the materials are quite rigid it may be difficult to use them as flexible plastic materials, such as plastic bags, so I expect they will be more suited for high-performance materials for optical, electronic, and biomedical applications,” Professor Toshifumi Satoh, the other corresponding author, adds.
Other research groups around the world are also exploring the potential for making plastic-replacing polymers from plants, and some such ‘bioplastics’ are already commercially available, but Satoh’s group has added a significant new opportunity to this fast-developing field.
The team now plans to explore further possibilities, but the feasible structural variations are so numerous that they would like to join forces with specialists in computational chemistry, artificial intelligence, and automated synthesis to explore the options.
“We hope this work will develop a wide variety of useful unnatural polysaccharide polymers to become part of a sustainable closed loop of synthesis from biomass with efficient recycling,” Li concludes.
4155/v