Special Refractory Produced in Iran for Gas Turbine Combustion Chambers
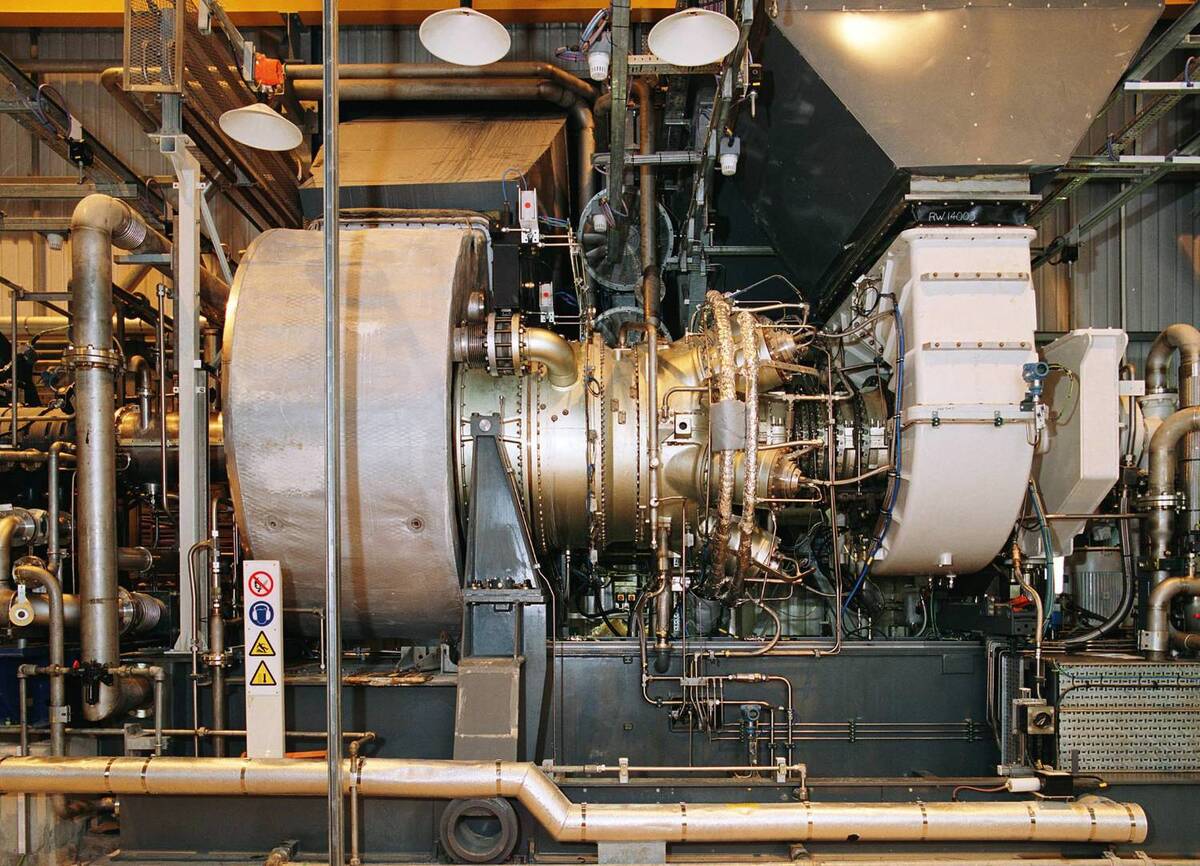
‘Atlasceram Kavir’ company has made the ceramic refractory matrix nanocomposite which successfully tolerates the elevated temperatures (from 1,100 to 1,850 K) and high pressures (from 5 to 10 atm).
It is highly corrosion-resistant, endures strong thermal shock, and benefits a long lifespan.
Adding hard nanoparticles to the ceramic matrix has resulted in increased mechanical strength, better dimensional accuracy, proper thermal shock resistance and longer lifetime at elevated temperatures and high pressures.
The refractory can be used in the internal walls of combustion chamber in gas turbines and it can also be utilized as crucibles and melt paths in ferrous and non-ferrous metals industries.
Earlier this year, researchers at an Iranian company had also used nanoparticles to produce a material for making steel parts which can be applied as a substitute for castings in steel plants as well as cement and petrochemical industries.
The patrocast produced in the company, which is usually mixed with the help of a fluid and poured into a specific holder to create a refractory piece, enjoys several advantages, including reasonable price, very high cold compressive strength, temperature tolerance from 1,400 to 1,850 degrees Celsius and reinforcement with nanoparticles with dimensions less than 50 nm.
Various binders, including colloidal binders, are used in the production of cast refractories. This product is a refractory castable mass or a cast containing nanoparticles, which is considered as a very suitable alternative to castable casts, and its high cold compressive strength is one of its distinctive features, and it tolerates heat from 1,400 to 1,850 degrees, depending on the percentage of alumina in the formula.
4155/v