Making Ammonia from Thin Air
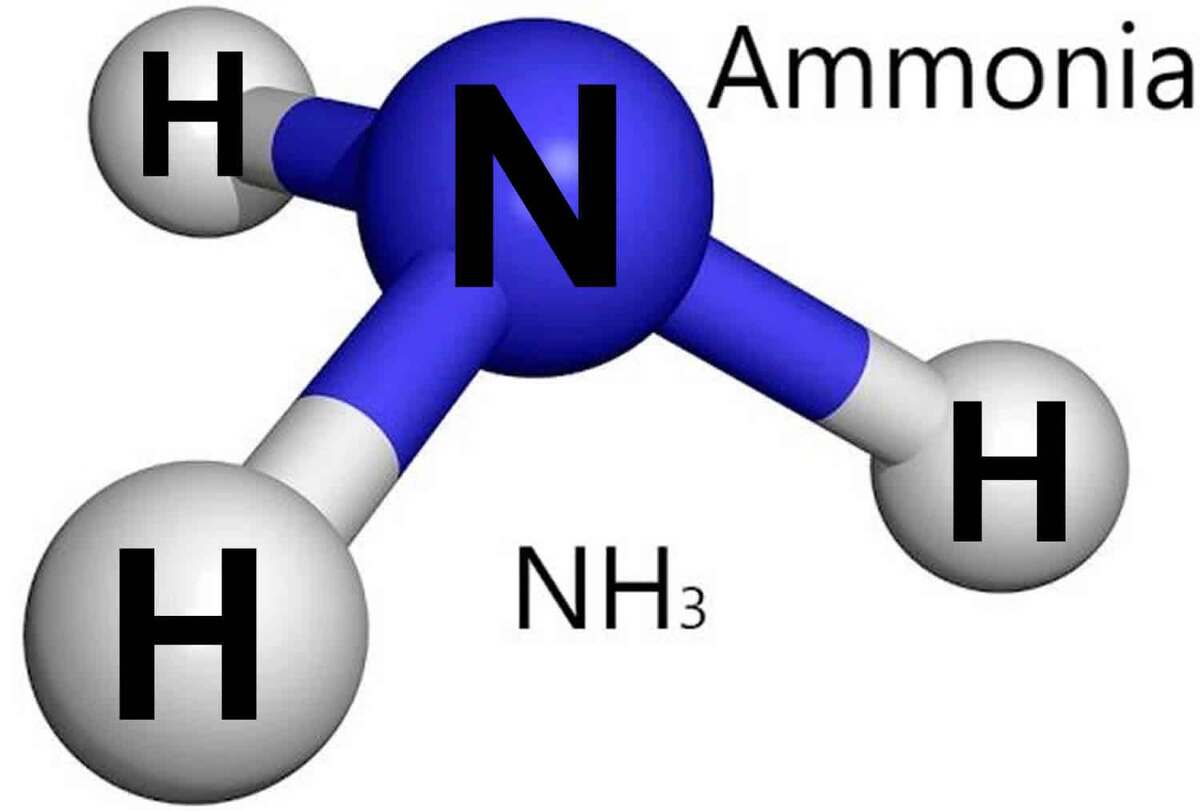
Currently, the annual production of ammonia is around 150M tonnes and carries a 0.8G ton CO2 footprint. Specifically, for every ton of ammonia production an energy input of around three Giga Joules is required. Derived from fossil resources, this amount of energy co-generates about five tonnes of CO2, corresponding to roughly 7% of all industrial greenhouse gas emissions, the journal PNAS reported.
In the Haber-Bosch process, ammonia is produced from nitrogen and hydrogen, and is enabled by an iron- or ruthenium-based solid-state catalyst driven at high temperature and pressure. Since its discovery, many other catalysts have been explored to reduce the extreme conditions of the process, but so far, to no avail.
The urgent need to displace the Haber-Bosch process with one that is less energy intensive and thus more environmentally friendly has inspired the use of renewable forms of energy to power electrical, light, and mechanical catalyst equivalents of the ammonia synthesis reaction. None so far have performance indicators (i.e., energy efficiency, reaction rate and selectivity, conversion yield, durability, scale, carbon intensity) that come close to replacing the Haber-Bosch process from its throne.
However, this might all change thanks to a remarkable discovery that ammonia can be synthesized in a one-step chemical reaction essentially from thin air! The reaction require no input of thermal, electrical, or solar energy.
In a recent study, scientists report that all one needs to produce ammonia is a jet of compressed air comprised mainly of nitrogen forced through a capillary water spray nozzle. This device creates a mist, effectively an aerosol comprised of micron-size water droplets containing a small amount of dissolved nitrogen. The mist collides with a porous graphite mesh coated with a film of iron oxide particles supported on an acidic polymer.
A mass spectrometric analysis of the molecular weights of the emergent mist of microdroplets reveals the presence of ammonia with some hydrazine (N2H4). Various water microdroplet control experiments under a range of spray operating conditions lacking nitrogen and without iron oxide on the mesh demonstrated they are key ingredients to make ammonia, eliminating false positives.
The generation of ammonia by this means, without assistance from an external electrical potential, heat, or light, was fast. It clocked at the sub-millisecond range with an estimated conversion rate in the nanomole per second range over an area of a square centimeter. The detection of hydrazine as a co-product suggests a reaction pathway involving the sequential protonation of nitrogen via hydrazine to produce ammonia. This reaction scheme is supported by quantum chemistry calculations.
The observed ammonia production rate is considered high while the conversion yield is low compared to ammonia syntheses reported in the literature using photocatalytic and electrocatalytic methods. From the information presently available, one can speculate that this process is assisted by some unique properties of the surface of the water microdroplets which allows electron transfer redox chemistry needed to facilitate the ammonia synthesis reaction. The contribution of each of these effects remains to be ascertained.
One can imagine that a scaled, efficient, robust, and cost-effective version of this aerosol ammonia synthesis process, if successfully implemented, could find world-wide applicability in the format of agricultural, ground and air fertilizer crop spraying machines, an innovation which holds promise for future sustainable and environmentally friendly food production and climate amelioration technology.
4155/v