Iranian Researchers Find New Way to Increase Corrosion Proof Feature in Composite Coatings
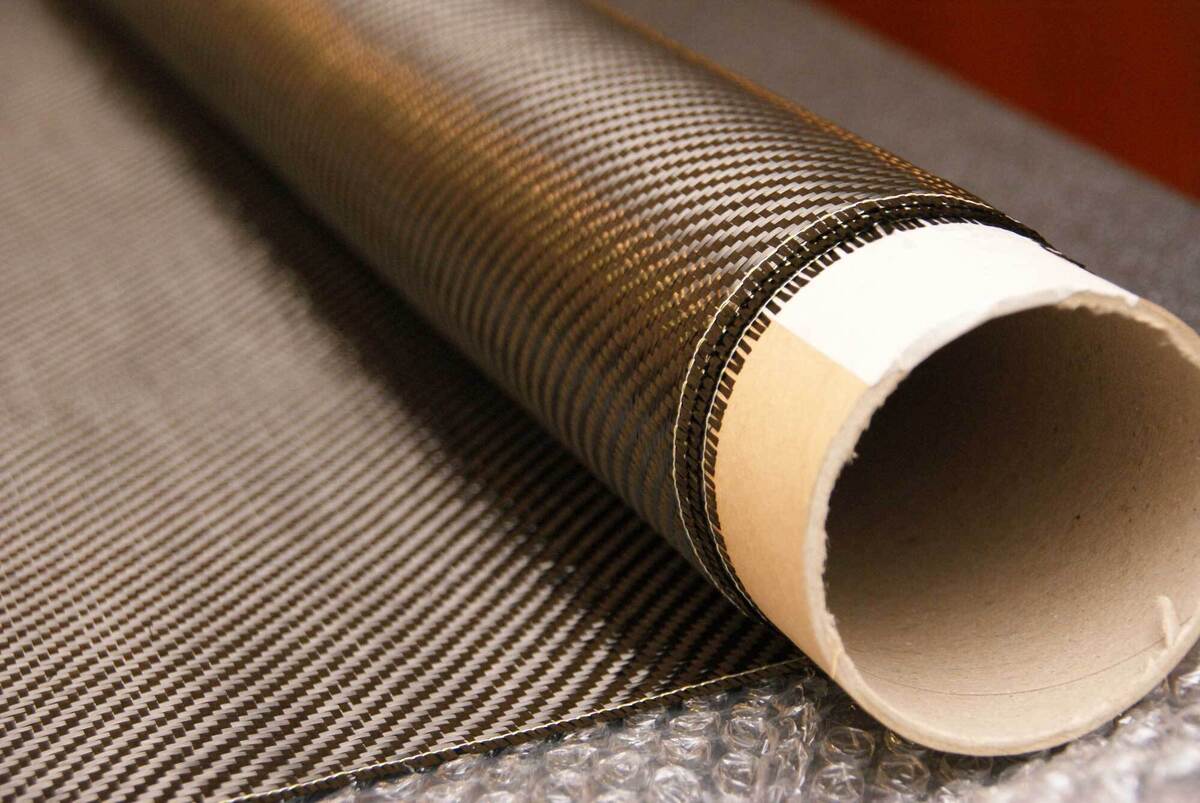
Nazanin Shakiba, is a Ph.D student at Amirkabir University of Technology (AUT) and executive director of the project to create and survey the corrosion properties of the composite coating in the Al-O-N system using plasma oxidation method (PEO) of alkaline aluminite electrolyte and inorganic-nitrogen complexes.
“’Normally, increasing the surface physico-chemical properties of metals is one of the most important reasons for changing engineering factors and modifying the surface of metals. In order to reduce the costs caused by corrosion and abrasion, many researchers modify the surface by placing a coating to make the metal parts corrosion proof, change the friction between opposite surfaces and change the abrasion mechanisms by changing the roughness and physical-chemical properties of the surface to improve the properties of the surfaces of metal parts,” Shakiba said.
"Due to the focus of this project on production of composite coatings in the Al-O-N system which had to contain aluminum nitrogenous oxygen phases resistant to environments with halide anions by plasma electrolytic oxidation (PEO) coating method, we used aluminum substrate as the work piece (anode)," she went on to say.
“We selected aluminum substrate due to the compatibility of the substrate and the oxide-based composite coating containing the aluminum oxynitride phases,” the UAT researcher said, adding, “In addition, 2000 series aluminum substrate has been used in order to discover the increase of corrosion resistance by this type of composite coating. This choice was also due to the abundance and low cost of this substrate and the very low corrosion resistance of this series from the aluminum family," Shakiba said.
“Light metals such as aluminum have a higher strength-to-weight ratio compared to iron due to their low density. For this reason, it is widely used in the aerospace and transportation industries,” Shakiba said, adding, “However, it generally has poor corrosion and abrasion properties. In order to increase the tribological and corrosion performance of this metal, surface coating is used to increase its wear and corrosion resistance properties.”
“Studying the tribological and abrasion properties of this type of coating can broaden its uses. Due to the very good mechanical properties of this type of composite coating, if this feature is studied, this coating can be used in tougher environmental and industrial conditions such as moving parts and in high temperature conditions and corrosive environments with halide anions such as chloride," the researcher said.
“Due to the identification of the mechanisms involved in the electrolytic coating method and as a result of obtaining the ability to produce aluminum oxynitride composite-ceramic coating in this research project, it is possible to change and control the parameters of the electrolyte and the process in the future. The raw materials used make more complex composite coatings (containing other light elements such as carbon and boron) with unique properties by this low cost and significant coating method compared to other expensive common methods of producing ceramic composite coatings to produced complex composite on metals.”
“Therefore, according to the findings of this research, it will be a big revolution in the approach and a new attitude to expand the use of the PEO method to produce different ceramic coatings with different and significant properties, while at a lower price,” the AUT researcher concluded.
4155/i