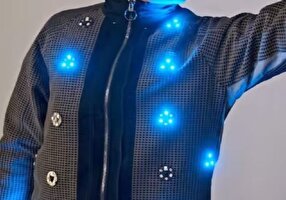
راهکارهای مدرن با لوله مانیسمان، سپتیک فاضلاب و پلیکا برای پروژههای حرفهای
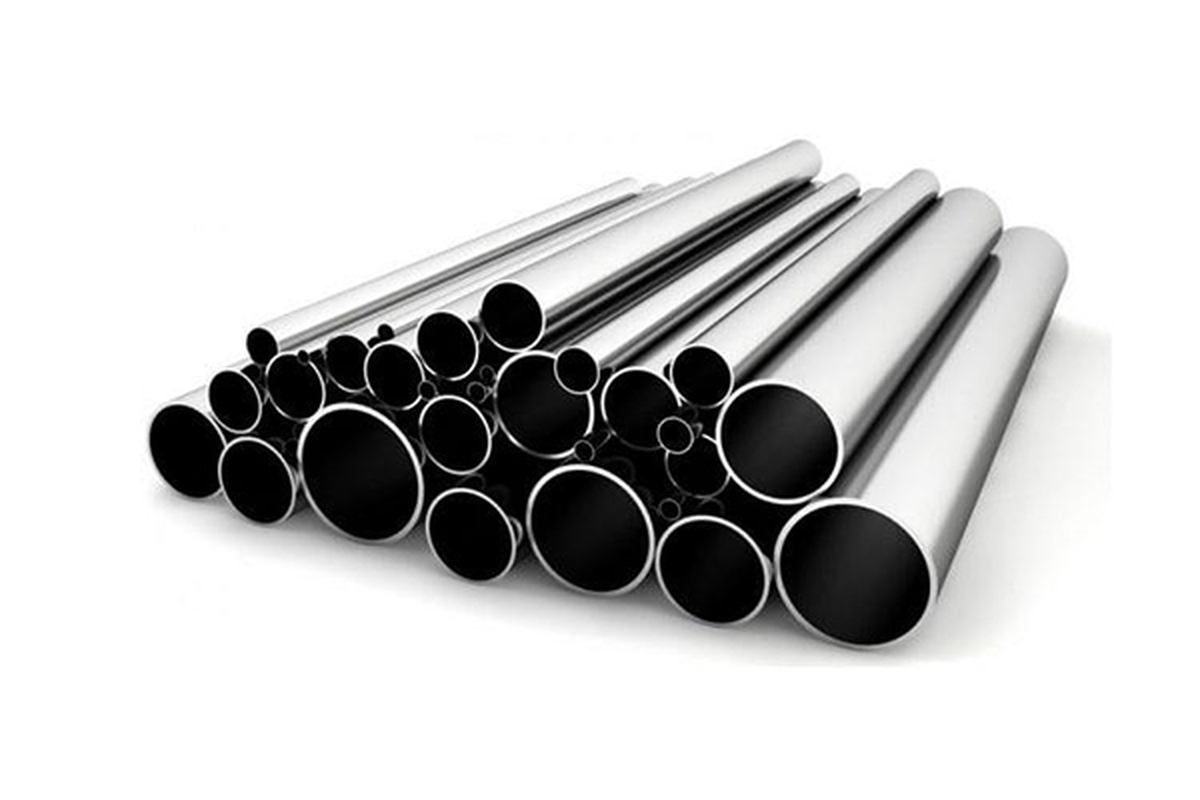
به گزارش گروه بازار خبرگزاری علم و فناوری آنا، خرید لوله مانیسمان یکی از گزینههای کلیدی در پروژههای ساختمانی و صنعتی است که به دلیل ویژگیهای منحصر به فردش، محبوبیت زیادی پیدا کرده است. لولههای مانیسمان به عنوان لولههای فولادی بدون درز شناخته میشوند و به دلیل مقاومت بالا در برابر فشار و استحکام زیاد، در پروژههای حساس و کاربردهای صنعتی از جمله صنایع نفت، گاز و پتروشیمی، انتخابی ایدهآل هستند. این لولهها برخلاف لولههای معمولی که بهوسیله جوشکاری به هم متصل میشوند، یکدست بوده و از استحکام و عمر بیشتری برخوردارند.
علاوه بر آن، لولههای پلیکا و کاروگیت نیز با کاربردهای مختلف در سیستمهای فاضلاب و آبرسانی، نقش مهمی در پروژههای مدرن ایفا میکنند. این لولهها با توجه به ویژگیهای خاص خود، بهویژه در سیستمهای فاضلاب و انتقال سیالات، گزینههای مقرون بهصرفه و کارآمدی هستند. استفاده از این لولهها در کنار سیستمهای سپتیک فاضلاب، میتواند بهطور مؤثری در کاهش هزینهها و افزایش بهرهوری پروژههای ساختمانی و عمرانی تاثیرگذار باشد.
معرفی کامل لوله مانیسمان
لوله مانیسمان نوعی لوله فولادی است که برخلاف سایر لولهها هیچ درز یا جوشکاری در بدنه خود ندارد. این ویژگی به دلیل فرآیند تولید خاصی است که در آن از شمشهای فولادی استفاده میشود و بدون نیاز به جوش، لوله یکدست تولید میشود. لوله مانیسمان بهطور گستردهای در صنایع مختلف مانند نفت و گاز، نیروگاهها، صنایع شیمیایی و غذایی کاربرد دارد. دلیل استفاده از این لولهها، استحکام بالای آنها، مقاومت در برابر فشار و ضربه، عمر طولانی و امکان انتقال سیالات بدون افت فشار است.
لوله مانیسمان به نام مخترعان آن، برادران آلمانی رینهارد و مکس مانیسمان نامگذاری شده است. این اختراع در سال 1885 در آلمان به ثبت رسید و تحولی بزرگ در صنعت لولهسازی و مهندسی ایجاد کرد. با اختراع فرآیند نورد بدون درز، امکان تولید لولههایی با بدنهای یکپارچه فراهم شد که در مقایسه با لولههای درزدار مقاومت و کیفیت بالاتری دارند. این فناوری همچنان به عنوان فرآیند مانیسمان شناخته میشود.
ولههای مانیسمان برخلاف لولههای درزدار، هیچگونه اتصال جوشی ندارند. این امر باعث میشود که لولههای مانیسمان از نظر مقاومت مکانیکی و تحمل فشار بسیار قویتر از لولههای درزدار باشند. همچنین، فرآیند تولید لولههای مانیسمان پیچیدهتر و گرانتر از لولههای درزدار است. لولههای درزدار به دو نوع درز مستقیم و درز مارپیچ تقسیم میشوند که نسبت به لولههای مانیسمان استحکام کمتری دارند و بیشتر برای کاربردهای سادهتر مورد استفاده قرار میگیرند.
بررسی مشخصات و ویژگیهای لولههای مانیسمان
لولههای مانیسمان یا لولههای بدون درز، به دلیل ویژگیهای فنی خاص خود، انتخاب مناسبی برای استفاده در صنایع مختلف به شمار میروند. این لولهها بهویژه در انتقال مایعات و گازها با فشار و دماهای بالا بسیار کارآمد هستند و به دلیل عدم وجود درز یا جوشکاری، از استحکام بالایی برخوردارند.
یکی از مهمترین ویژگیهای لولههای مانیسمان، فشار کاری آنها است که بسته به سایز، ضخامت و دمای کاری لوله تعیین میشود. برای هر لوله، جداول استانداردی برای فشار کاری در دماها و سایزهای مختلف وجود دارد که مشخص میکند لوله میتواند در چه فشارهایی استفاده شود. ضخامت لولههای مانیسمان نیز اهمیت زیادی دارد و معمولاً در ردههای ۲۰، ۴۰ و ۸۰ عرضه میشود. رده ۲۰ معمولاً برای کاربردهای سبکتر و رده ۸۰ برای شرایط پرفشار و خورندگی استفاده میشود.
لولههای مانیسمان طبق استانداردهای بینالمللی مختلفی از جمله ASTM، JIS و DIN تولید میشوند. این استانداردها برای انواع مختلف لولههای فولادی و استیل، مانند ASTM A106 (مناسب برای دماهای بالا) و ASTM A192 (مناسب برای دیگهای بخار)، به کار میروند. این استانداردها تضمینکننده کیفیت و کارایی بالای لولههای مانیسمان در شرایط مختلف هستند.
بررسی مشخصات فنی لولههای مانیسمان
مشخصات فنی لولههای مانیسمان طبق استانداردهای جهانی تعریف میشود و به طور عمده از دو استاندارد ASME B36.10 برای لولههای فولادی و ASME B36.19 برای لولههای استیل پیروی میکنند. این استانداردها بازههایی برای مشخصات لولهها نظیر قطر، ضخامت، طول و فشار کاری تعیین کردهاند که تولیدکنندگان باید مطابق با آنها عمل کنند. مشخصات فنی لولههای مانیسمان را در زیر مشاهده میکنید:
- قطر و ضخامت: لولههای مانیسمان در اندازهها و ضخامتهای مختلف تولید میشوند. قطر این لولهها از 1.2 اینچ آغاز و تا 20 اینچ یا بیشتر نیز میتواند برسد. با افزایش قطر، ظرفیت انتقال سیالات بیشتر میشود و همچنین مقاومت لوله در برابر فشار و ضربه افزایش مییابد.
- آلیاژها: لولههای مانیسمان معمولاً از آلیاژهای مختلف فولادی و استیل تولید میشوند که برخی از آلیاژهای پرکاربرد را در زیر میبینید:
- ASTM A106: برای استفاده در دماهای بالا.
- ASTM A179: دارای کربن کم، مناسب برای کندانسرها.
- ASTM A192: مناسب برای دیگهای بخار.
- GB 3087: برای بویلرها کاربرد دارد.
- فشار کاری: فشار کاری لولههای مانیسمان به عوامل مختلفی از جمله قطر، ضخامت و دمای کاری بستگی دارد. در این لولهها، فشار کاری بر اساس استانداردهای مختلف مشخص میشود و باید در حین استفاده به آن توجه ویژهای شود.
- طول و اندازه: لولههای مانیسمان معمولاً در طولهای 6 متر و 12 متر تولید میشوند. طول 6 متر از نظر هزینه و کاربرد، محبوبتر است و مقرون به صرفهتر است.
- استحکام و مقاومت: لولههای مانیسمان به دلیل ساخت بدون درز، مقاومت بالایی در برابر فشار و خوردگی دارند که این ویژگی باعث میشود در صنایع مختلف مانند نفت، گاز، پتروشیمی و ساخت و ساز بسیار محبوب باشند.
در نهایت، با توجه به ویژگیهای فنی دقیق و استانداردهای بینالمللی، خرید لوله مانیسمان انتخابی عالی برای استفاده در شرایط دشوار و محیطهای صنعتی با فشار بالا و نیاز به مقاومت زیاد به حساب میآید.
مهمترین کاربردهای لوله مانیسمان
برخی از مهمترین کاربردهای لوله مانیسمان را در زیر مشاهده میکنید:
- صنایع نفت و گاز: لولههای مانیسمان در خطوط انتقال نفت، گاز و سوختهای فسیلی به کار میروند. این لولهها به دلیل مقاومت در برابر فشار و خوردگی، گزینهای ایدهآل برای استخراج و انتقال نفت و گاز در محیطهای مرطوب و سخت هستند.
- صنایع پتروشیمی: لولههای مانیسمان در صنایع پتروشیمی برای انتقال مواد شیمیایی و گازهای صنعتی استفاده میشوند. استحکام بالای این لولهها باعث میشود که در محیطهای شیمیایی و صنعتی که فشار و دما بالاست، به خوبی عمل کنند.
- مبدلهای حرارتی و گرمایی: لولههای مانیسمان در سیستمهای مبدل حرارتی و گرمایی به کار میروند، جایی که نیاز به انتقال حرارت در شرایط فشار بالا وجود دارد. این لولهها قادر به تحمل دماهای بالا و شرایط فشاری سخت هستند.
- نیروگاهها و خطوط فشار قوی: در نیروگاهها، برای انتقال انرژی و همچنین در خطوط انتقال برق فشار قوی، لولههای مانیسمان به دلیل مقاومت بالایشان در برابر شرایط سخت استفاده میشوند.
- صنایع غذایی و دارویی: لولههای مانیسمان استیل در صنایع غذایی و دارویی برای انتقال مواد خوراکی و دارویی به کار میروند. این لولهها به دلیل ویژگیهای بهداشتی و مقاومت در برابر خوردگی، مناسب برای حمل مواد حساس هستند.
- آبرسانی و کشاورزی: لولههای مانیسمان در سیستمهای آبرسانی صنعتی و کشاورزی نیز کاربرد دارند. مقاومت بالا در برابر رطوبت و خوردگی، این لولهها را برای استفاده در شرایط سخت و مرطوب ایدهآل میسازد.
- صنعت خودروسازی: لولههای مانیسمان در بخشهای مختلف خودرو مانند سیستم اگزوز، انتقال سوخت و بدنه خودرو به کار میروند. مقاومت بالا در برابر فشار و خوردگی از ویژگیهایی است که این لولهها را در صنعت خودروسازی بسیار مفید میسازد.
- سیستمهای آتشنشانی: لولههای مانیسمان به دلیل مقاومت بالا در برابر حرارت و فشار، در سیستمهای آتشنشانی به کار میروند تا سیالات آتشنشانی را به طور ایمن و مؤثر انتقال دهند.
نحوه ساخت لوله مانیسمان به چه صورتی است؟
لوله مانیسمان با استفاده از تکنیک خاصی به نام بیرونآمدگی یا Extruding تولید میشود. فرآیند تولید این لولهها از مراحل مختلفی تشکیل شده است که در ادامه شرح داده میشود:
- آمادهسازی مواد اولیه: برخلاف لولههای درزدار که از ورق فولادی ساخته میشوند، لولههای مانیسمان از شمش فولادی یا مقاطع چهارگوش فولادی ساخته میشوند. این مواد اولیه وارد کارخانه شده و با توجه به سایز و مشخصات مورد نیاز، برای مرحله بعد آماده میشوند.
- برش و گرمادهی شمش: شمشها در سایزهای مخصوص برش داده میشوند و سپس وارد کورههای قوسی میشوند تا به درجه حرارت مناسب برسند. این فرآیند باعث نرم شدن شمشها میشود تا شکلدهی به آنها امکانپذیر باشد.
- سُنبهکاری چرخشی: پس از گرمادهی، از فرآیند سُنبهکاری چرخشی استفاده میشود که باعث تبدیل شمش به شکل یک لوله میشود. این مرحله یکی از مهمترین مراحل در تولید لوله مانیسمان است.
- تابگیری و تنظیم سر و ته شمش: پس از سُنبهکاری، لوله به شکل کاملتری درمیآید و لازم است که تابگیری و تنظیم سر و ته شمش انجام شود. در این مرحله، ابعاد و سایز نهایی لولهها مشخص میشود.
- تکمیل تولید و بستهبندی: در این مرحله، لولهها تحت آزمایش و بازرسی قرار میگیرند. لولههایی که ضایعات ندارند، در ابعاد مختلف برش داده شده و بستهبندی میشوند.
- روشهای جدید: با پیشرفت تکنولوژی، روشهای جدیدتری مانند ریختهگری گریز از مرکز یا پاششی برای تولید لولههای مانیسمان بهکار گرفته شدهاند که موجب افزایش کیفیت تولیدات میشوند.
این فرآیند باعث میشود که لولههای مانیسمان نسبت به لولههای درزدار از مقاومت بالاتری برخوردار باشند، زیرا لولههای مانیسمان هیچگونه درز یا جوشکاری ندارند که ممکن است باعث ضعف در برابر فشار و سیالات شود.
مزایای خرید لوله مانیسمان
برخی از مهمترین مزایای خرید و استفاده از لوله مانیسمان را در زیر نام بردهایم:
- استحکام و دوام بالا: لولههای مانیسمان به دلیل طراحی بدون درز خود، قادر به تحمل فشار و تنشهای مکانیکی بالا هستند و در شرایط سخت عملکرد عالی دارند. این ویژگیها آنها را به انتخابی ایدهآل برای صنایع نفت، گاز، پتروشیمی و خودروسازی تبدیل کرده است.
- مقاومت در برابر خوردگی: لولههای مانیسمان مقاومت بالایی در برابر زنگ زدگی و خوردگی دارند. به ویژه در محیطهای مرطوب یا شرایط شیمیایی دشوار، این لولهها عملکرد بهتری دارند و نیاز به تعویض یا تعمیر کمتری دارند.
- مقاومت در برابر دماهای بالا: این لولهها توانایی تحمل دماهای بالا را دارند و در صنایع و کاربردهایی که به دماهای زیاد نیاز دارند، مانند صنایع پتروشیمی و نفت، بسیار مناسب هستند.
- یکپارچگی ساختاری: به دلیل عدم وجود درز جوش در لولههای مانیسمان، این لولهها از یکنواختی بالایی برخوردار هستند که باعث کاهش اصطکاک و بهبود جریان سیالات و گازها میشود.
- طول عمر بالا و پایداری در شرایط مختلف: لولههای مانیسمان عمر طولانی دارند و به دلیل استحکام بالا در برابر تغییرات دما و فشار، در شرایط بحرانی نیز عملکرد قابل اعتماد دارند.
- قابلیت بازیافت و دوستدار محیط زیست: لولههای مانیسمان از مواد قابل بازیافت تولید میشوند و به همین دلیل از نظر محیط زیستی نیز مناسب هستند.
در مجموع، خرید و استفاده از لوله مانیسمان به دلیل ویژگیهای مکانیکی و فنی برتر، گزینهای ایدهآل برای استفاده در صنایع حساس و شرایط سخت به شمار میآید.
معایب استفاده از لوله مانیسمان
استفاده از لولههای مانیسمان با وجود مزایای فراوانی که دارند، معایبی نیز به همراه دارد که باید در نظر گرفته شوند. این معایب را در زیر مشاهده میکنید:
- قیمت بالا: یکی از مهمترین معایب لولههای مانیسمان، قیمت بالای آنها است. فرآیند تولید پیچیدهتر و کیفیت بالاتر این لولهها باعث میشود که هزینه تولید آنها نسبت به لولههای درزدار بیشتر باشد. این مسئله ممکن است برای پروژههای بزرگ با بودجه محدود یک چالش باشد.
- وزن زیاد: لولههای مانیسمان به دلیل ضخامت و استحکام بالایی که دارند، وزن بیشتری نسبت به لولههای درزدار دارند. این امر میتواند در مراحل نصب و جابجایی این لولهها مشکل ایجاد کند و نیاز به تجهیزات خاص برای حمل و نصب داشته باشد.
- نیاز به نصب حرفهای: نصب لولههای مانیسمان به دلیل ویژگیهای خاص آنها، نیازمند تخصص و تجربه است. اگر نصب این لولهها به درستی انجام نشود، میتواند مشکلاتی مانند نشتی یا کاهش کارایی در طول زمان ایجاد کند. بنابراین، باید از تکنسینهای مجرب برای نصب استفاده کرد.
بررسی انواع لولههای مانیسمان
لولههای مانیسمان بر اساس عوامل مختلفی مانند جنس، روش تولید و کاربرد تقسیمبندی میشوند.
-
انواع لوله مانیسمان بر اساس جنس
لولههای مانیسمان در جنسهای مختلفی تولید میشوند. برخی از این جنسها عبارتند از فولاد، آلومینیوم، برنج و مس، هستند. این تنوع جنس باعث میشود که لولههای مانیسمان در صنایع مختلف با نیازهای متفاوت مورد استفاده قرار گیرند.
-
نواع لوله مانیسمان بر اساس روش تولید
لولههای مانیسمان براساس فرآیند تولید به دستههای مختلف تقسیم میشوند:
- اکسترود شده: در این روش، مواد به شکل یک لوله با فشار از قالب خارج میشوند.
- کشیده شده: این روش به لولههایی اطلاق میشود که از طریق کشش مواد تولید میشوند.
- درز هلیکال: در این نوع، لولهها با پیچش مواد در زاویهای خاص تولید میشوند.
-
ردههای مختلف لوله مانیسمان
لولههای مانیسمان در ردههای مختلفی از نظر ضخامت و وزن تولید میشوند که برخی از رایجترین ردهها را در زیر مشاهده میکنید:
- رده 20: این لولهها ضخامت بین 2 تا 6 میلیمتر و سایز 1 تا 12 اینچ دارند و وزن آنها ممکن است تا 300 کیلوگرم برسد.
- رده 40: این لولهها در سایز 1 تا 12 اینچ و ضخامت بین 2 تا 10 میلیمتر تولید میشوند. وزن این لولهها گاهی تا 500 کیلوگرم میرسد.
- رده 60: این لولهها معمولاً در قطرهای بین 8 تا 24 اینچ تولید میشوند و به دلیل بدون درز بودن و ضخامت بالای آنها تقاضای کمتری دارند.
- رده 80: لولههایی با ضخامت بین 3 تا 9 میلیمتر که در سایزهای متنوع تولید میشوند و وزن آنها معمولاً بین 9 تا 150 کیلوگرم است.
- رده 120: این لولهها معمولاً در سایز و ضخامتهای مختلف تولید میشوند و وزن آنها ممکن است تا 700 کیلوگرم نیز برسد.
- رده 160: این رده بالاترین وزن را دارد و معمولاً در صنایع خاص مانند پتروشیمی و صنایع نظامی کاربرد دارند.
معرفی کامل لولههای پلیکا
لوله پلیکا یا پلی وینیل کلراید غیر پلاستیک شده U-PVC یکی از انواع لولههای پلیمری است که بهطور گسترده در صنعت ساختمانسازی، کشاورزی و دیگر صنایع مورد استفاده قرار میگیرد. این لولهها از ماده اولیه PVC ساخته میشوند، اما برخلاف PVC معمولی که نرمکنندههای شیمیایی دارد، لولههای پلیکا بدون افزودن مواد نرمکننده تولید میشوند، بنابراین دارای ویژگیهای سختتری هستند. به همین دلیل، این لولهها بهعنوان لولههای PVC سخت شناخته میشوند. از ویژگیهای مهم لولههای پلیکا میتوان به موارد زیر اشاره کرد:
- دوام بالا: لولههای پلیکا بهخاطر مقاومت زیاد در برابر خوردگی و زنگزدگی و همچنین عمر طولانیتری که دارند، بهعنوان جایگزینی مناسب برای لولههای فلزی استفاده میشوند.
- مقاومت در برابر فشار: این لولهها میتوانند فشارهای مختلف را تحمل کرده و برای سیستمهای آبرسانی، فاضلاب و حتی سیستمهای تحت فشار به کار روند.
- ضد صدا: یکی از ویژگیهای برجسته لولههای پلیکا، کاهش صداهای مزاحم است که به خصوص در سیستمهای فاضلاب مهم است.
- مقاومت در برابر مواد شیمیایی: لولههای پلیکا مقاومت خوبی در برابر انواع مواد شیمیایی دارند و برای حمل و نقل مواد شیمیایی یا فاضلابها مناسب هستند.
این لولهها در دو نوع اصلی PVC و U-PVC در بازار موجود هستند و بسته به نیاز پروژه، میتوان از انواع مختلف آنها استفاده کرد. لولههای پلیکا به دلیل قیمت مناسب و نصب آسان، از محبوبیت زیادی در میان مصرفکنندگان برخوردارند و در بسیاری از پروژههای ساختمانی و صنعتی بهکار میروند.
لوله پلیکا چگونه تولید میشود؟
تولید لولههای پلیکا از طریق فرآیندهای مختلفی انجام میشود که هدف از آن تولید محصولاتی با کیفیت بالا و مطابق با استانداردهای بینالمللی است. در زیر، مراحل اصلی تولید این لولهها توضیح داده شده است:
- استفاده از پودر PVC خام: برای تولید U-PVC، از پودر PVC خام استفاده میشود. این پودر تحت فرآیندهای خاص فشاری و دمایی قرار میگیرد تا به شکل نهایی خود درآید. مواد اولیه بهدقت انتخاب و ترکیب میشوند تا ویژگیهای مطلوبی چون سختی و مقاومت در برابر فشار و خوردگی فراهم شود.
- روش اکستروژن: یکی از متداولترین روشهای تولید لولههای پلیکا، فرآیند اکستروژن است. در این روش، پودر PVC به دستگاه اکسترودر وارد میشود، جایی که با استفاده از گرما و فشار به یک حالت خمیری در میآید. سپس این ماده ذوبشده از قالب مخصوص عبور داده میشود تا به شکل لولهای پیوسته درآید. این روش به دلیل سهولت اجرا و کیفیت بالای محصول نهایی بسیار محبوب است.
- روش پوششدهی دورانی: در این روش، U-PVC توسط دستگاههای خاصی با حرکت دورانی تولید میشود. این فرآیند بیشتر برای تولید لولههای با قطرهای بزرگ و مقاومت مکانیکی بالا استفاده میشود. در این روش، لولهها بهطور مداوم تحت فشار و گرما قرار گرفته و لایههای محافظتی به آنها افزوده میشود.
- وش تزریق یا فشاری: در این فرآیند، مواد PVC با فشار به داخل قالبهای مخصوص تزریق میشوند. این روش برای تولید لولههای کوچکتر با جزئیات دقیقتر و ظریفتر مناسب است. در این فرآیند، فشار بهطور یکنواخت به مواد وارد شده تا قالبها به درستی پر شوند.
در تمام این مراحل، نظارت دقیق بر متغیرهای مختلف مانند دما، فشار و سرعت تولید، توسط مهندسان و مدیران کارخانه انجام میشود تا محصولات نهایی با کیفیت بالا و مطابق با استانداردهای جهانی تولید شوند.
لولههای پلیکا چه کاربردهایی دارند؟
لولههای پلیکا به دلیل ویژگیهایی جذاب، کاربردهای گستردهای دارند. برخی از مهمترین کاربردهای این لوله را در زیر مشاهده میکنید:
- سیستم آبرسانی و فاضلاب ساختمان: لولههای پلیکا بهعنوان یک گزینه مطمئن در انتقال آب و فاضلاب در ساختمانها استفاده میشوند. این لولهها بهویژه برای سیستمهای فاضلاب داخلی بسیار مناسب هستند.
- سیستم تهویه و برودتی ساختمانها: لولههای پلیکا در سیستمهای تهویه و برودتی ساختمانها به دلیل انعطافپذیری و ویژگیهای اجرایی ساده، بهطور گستردهای کاربرد دارند.
- صنعت و شهرسازی: در پروژههای صنعتی و ساخت و ساز شهری، لولههای پلیکا برای انتقال مواد و سیالات مختلف مورد استفاده قرار میگیرند.
- انتقال فاضلاب شرکتهای صنعتی: این لولهها به دلیل مقاومت بالا در برابر مواد شیمیایی و شرایط محیطی مختلف، برای انتقال فاضلاب در صنایع مختلف بسیار مناسب هستند.
- حمایت و عایقسازی سیستمهای برقی و مخابراتی: لولههای پلیکا بهعنوان پوشش برای کابلهای برق و مخابرات استفاده میشوند تا از آسیب دیدن سیمها و کابلها جلوگیری کرده و امنیت بیشتری فراهم کنند.
- آبیاری تحت فشار: در کشاورزی، لولههای پلیکا برای سیستمهای آبیاری تحت فشار در زمینهای کشاورزی، باغها و گلخانهها کاربرد دارند.
- پوشش کابلهای شبکه برق و نیرو: لولههای پلیکا بهعنوان پوشش برای کابلهای برق در شبکههای برقی و مخابراتی استفاده میشوند تا از خطرات احتمالی مانند برقگرفتگی جلوگیری کند.
بررسی انواع لولههای پلیکا
لولههای پلیکا از متریالهایی هستند که در انواع مختلف با ویژگیها و کاربردهای متفاوت در ساختمانها و صنایع مختلف استفاده میشوند. در ادامه به بررسی انواع لولههای پلیکا میپردازیم:
-
فشار ضعیف یا معمولی
این نوع لولهها که به لولههای پلیکا فشار ضعیف نیز معروف هستند، کمضخامتترین و سبکترین نوع لوله پلیکا به شمار میآیند. این لولهها مقاومت کمی در برابر فشار دارند و به همین دلیل برای استفاده در مناطقی که تحمل فشار بالایی نیاز نیست، مناسب هستند. همچنین این نوع لوله به عنوان عایق صوتی نیز مناسب نیست.
-
نیمه قوی یا فشار متوسط
لولههای پلیکا نیمه قوی که به لولههای فشار متوسط نیز شناخته میشوند، از لولههای پلیکا معمولی مقاومتر هستند و برای کاربردهایی که نیاز به تحمل فشار بیشتری دارند، مناسباند. این لولهها مقاومت خوبی در برابر فشار و ضربه دارند و در بسیاری از مواقع برای عایقسازی سیستم برق کشی نیز به کار میروند.
-
فشار قوی
لولههای پلیکا فشار قوی به عنوان یکی از مقاومترین انواع لولههای پلیکا شناخته میشود. این لولهها معمولاً در بخشهایی که نیاز به انتقال سیالات با فشار بالا یا انتقال مواد خطرناک مانند اسیدها و بازها دارند، به کار میروند. لولههای فشار قوی در صنایع بزرگ و شرکتهای صنعتی که نیاز به سیستمهای لولهکشی مقاوم در برابر ضربه و فشار دارند، استفاده میشوند. این لولهها برای پوششدهی و عایقکاری لولههای دیگر در مناطقی که خطر آسیبدیدگی وجود دارد نیز به کار میروند.
-
انواع لولههای پلیکا بر اساس سایز و اندازه
لولههای پلیکا در اندازههای مختلفی تولید میشوند. از جمله سایزهای معمول لولههای پلیکا میتوان به 20، 25، 32، 40، 50، 63، 75، 90، 110، 125، 160، 200، 250، 315، 350، 400، 500 و 630 میلیمتر اشاره کرد. این اندازهها به طور معمول بر اساس نیاز پروژههای مختلف انتخاب میشوند.
معرفی کامل لولههای کاروگیت چیست
لولههای کاروگیت پلیاتیلن یکی از انواع لولههای پلیمری با ویژگیهای منحصر به فرد هستند که در بسیاری از پروژههای فاضلابی و سیستمهای زهکشی شهری و صنعتی کاربرد دارند. این لولهها به دلیل طراحی خاص خود، به نامهای مختلفی از جمله لولههای دو جداره فاضلابی، لولههای آکاردئونی، لوله خرطومی فاضلاب و لوله اسپیرال مسلح شناخته میشوند.
بررسی ویژگیهای لولههای کاروگیت
لولههای کاروگیت به دلیل ویژگیهای خاص خود، یکی از بهترین گزینهها برای استفاده در سیستمهای فاضلابی و انتقال آبهای سطحی به شمار میروند. این لولهها با داشتن دو جداره مجزا، ویژگیهای زیر را دارند که آنها را از دیگر انواع لولهها متمایز میکند:
- عمر طولانی: لوله کاروگیت به دلیل استفاده از مواد مقاوم مانند پلی اتیلن با دانسیته بالا دارای طول عمر بالا و دوام زیادی در شرایط مختلف محیطی است.
- انعطافپذیری: طراحی خاص لولههای کاروگیت موجب انعطافپذیری بالای آنها شده که این ویژگی باعث میشود تا در برابر فشارهای خارجی و تغییرات محیطی مقاوم باشند.
- تعمیر و نگهداری آسان: لولههای کاروگیت به راحتی نصب، تعمیر و نگهداری میشوند. ساختار ساده و مقاوم آنها باعث کاهش نیاز به تعمیرات مداوم میشود.
- ضریب اصطکاک بسیار پایین: سطح داخلی صاف و صیقلی لولههای کاروگیت موجب کاهش اصطکاک و تسهیل جریان سیالات، به ویژه در سیستمهای فاضلابی میشود.
- سبکی وزن و حملونقل آسان: لولههای کاروگیت بسیار سبک هستند و حمل و نقل آنها به راحتی امکانپذیر است که این ویژگی باعث کاهش هزینههای نصب و جابجایی میشود.
- سرعت بالا در نصب و راهاندازی: نصب لولههای کاروگیت به دلیل وزن سبک و روشهای نوین اتصال، مانند جوش الکتروفیوژن، بسیار سریع و آسان انجام میشود.
- مقاومت در برابر اشعه ماورا بنفش: این لولهها در برابر تابش مستقیم نور خورشید و اشعه ماورا بنفش مقاوم هستند و دچار پوسیدگی یا تخریب نمیشوند.
- قابلیت جوش با الکتروفیوژن: لولههای کاروگیت قابلیت جوشکاری با روش الکتروفیوژن را دارند که این امر باعث اتصال محکم و مقاوم در برابر سایش میشود.
- مقاومت در برابر میکروارگانیسمها: این لولهها در برابر میکروبها و باکتریها مقاوم هستند و امکان تجزیه توسط آنها وجود ندارد.
- مقاومت بالا در برابر خوردگی و مواد شیمیایی: لولههای کاروگیت نسبت به مواد شیمیایی مختلف، از جمله اسیدها، نمکها و بازها مقاوم هستند و دچار خوردگی نمیشوند.
بررسی مشخصات فنی لوله کاروگیت
لولههای کاروگیت پلی اتیلنی برای استفاده در سیستمهای مختلف به ویژه فاضلابی و انتقال آبهای سطحی، باید استانداردهای خاصی را رعایت کنند تا از کیفیت و مقاومت مطلوب برخوردار باشند. در این راستا، مشخصات فنی این لولهها بر اساس آزمایشات متعدد و استانداردهای بینالمللی و داخلی تعیین میشود. برخی از مهمترین این استانداردها را در زیر نام بردهایم:
- آزمون چگالی: مواد اولیه باید دارای استاندارد ISIRI175-5 باشد و محصول نهایی باید استاندارد ISIRI9116 را رعایت کند. این استانداردها برای اطمینان از چگالی و استحکام پلی اتیلن به کار میروند.
- آزمون شاخص جریان مذاب MFI: لولههای تولیدی باید از مواد اولیهای با شاخص جریان مذاب مطابق استانداردهای ISIRI6980 و ISIRI9116 ساخته شوند. این شاخص نشاندهنده جریانپذیری مواد در حین تولید و کیفیت تولید لولهها است.
- آزمون مقاومت حلقوی بلند مدت: باید مقاومت مناسبی در برابر فشارهای خارجی داشته باشند. این مقاومت طبق استانداردهای ISIRI9110 و DIN1961 تایید میشود.
- آزمون مقاومت حلقوی کوتاه مدت: برای سنجش مقاومت لولهها در برابر فشارهای ناگهانی، از استانداردهای ISIRI9116 و ISO 9969 استفاده میشود.
- آزمون انعطافپذیری: میزان انعطافپذیری لولههای کاروگیت باید طبق استانداردهای ISIRI9116 و EN1446 ارزیابی گردد تا از انعطاف کافی برای نصب و تحمل تغییرات محیطی اطمینان حاصل شود.
- آزمون میزان دوده: درصد دوده موجود در لولههای کاروگیت طبق استانداردهای ISIRI7175-2 و ISIRI9116 تعیین میشود که بر کیفیت مقاومت در برابر شرایط محیطی تاثیر دارد.
- آزمون پراکنش دوده: پراکنش یکنواخت دوده در لوله باید طبق استانداردهای ISIRI7175-6 و ISIRI9116 بررسی شود.
- آزمون مقاومت در برابر ضربه: لولههای کاروگیت باید از مقاومت کافی در برابر ضربه برخوردار باشند که این ویژگی طبق استانداردهای ISIRI9116 و EN744 تایید میشود.
- آزمون بازگشت حرارتی: لولهها باید طبق استانداردهای ISIRI9116 و ISIRI7175-3 در برابر تغییرات حرارتی مقاوم باشند.
- آزمون کشش خطی: لولههای کاروگیت باید مقاومت مناسبی در برابر کشش داشته باشند که طبق استانداردهای ISIRI9116 و EN1979 تایید میشود.
معرفی تمامی کاربردهای لولههای کاروگیت
لولههای کاروگیت پلیاتیلنی بهدلیل ویژگیهای خاص خود، در صنایع مختلف و پروژههای شهری و روستایی کاربردهای فراوانی دارند. این لولهها با ساختار دو جداره و شیارهای خاص خود، گزینهای ایدهآل برای انتقال سیالات و مواد مختلف از زیر زمین به شمار میروند. مهمترین کاربردهای لوله کاروگیت را در زیر مشاهده میکنید:
- سیستمهای جمعآوری و انتقال فاضلاب: لولههای کاروگیت بهویژه در پروژههای فاضلاب شهری و روستایی کاربرد زیادی دارند. این لولهها با داشتن سطح داخلی صاف و مقاوم در برابر خوردگی، برای انتقال فاضلابهای خانگی و صنعتی مناسب هستند.
- سیستمهای زهکشی: لولههای کاروگیت در پروژههای زهکشی در زمینهای کشاورزی، ساختمانی و پروژههای عمرانی برای هدایت آبهای سطحی یا آبهای زیرزمینی استفاده میشوند.
- انتقال آب باران: این لولهها بهطور خاص در سیستمهای جمعآوری آب باران کاربرد دارند و بهعنوان لولههای زهکش برای جلوگیری از جمعشدن آبهای سطحی مورد استفاده قرار میگیرند.
- سیستمهای آبیاری: لولههای کاروگیت بهویژه در آبیاری کشاورزی، از جمله آبیاری قطرهای، بهعنوان لولههای انتقال آب مورد استفاده قرار میگیرند. انعطافپذیری این لولهها در انتقال آب در زمینهای با شیب ملایم بهویژه در کشاورزی مفید است.
- انتقال مواد شیمیایی: این لولهها بهدلیل مقاومت بالا در برابر مواد شیمیایی مانند اسیدها و بازها، برای انتقال مواد صنعتی و شیمیایی در کارخانهها و صنایع مختلف مناسب هستند.
- ساخت منهولها: لولههای کاروگیت در ساخت منهولها برای سیستمهای جمعآوری آب و فاضلاب مورد استفاده قرار میگیرند. این لولهها بهدلیل مقاومت و انعطافپذیری بالا، انتخابی مناسب برای این نوع پروژهها هستند.
- ساخت مخازن ذخیره مایعات: لولههای کاروگیت در ساخت مخازن ذخیرهسازی آب و سایر مایعات کاربرد دارند. این لولهها بهویژه برای ذخیرهسازی آب در مناطق خشک و کمآب مفید هستند.
- انتقال آبهای سطحی و رودخانهها: لولههای کاروگیت در پروژههای بزرگتر، مانند انتقال آب از رودخانهها و سفرههای آب سطحی، برای هدایت آبهای طبیعی استفاده میشوند.
معرفی کامل و دقیق سپتیک فاضلاب
سپتیک تانک یا چاه سپتیک یکی از سیستمهای زیرزمینی تصفیه فاضلاب است که در مناطقی که به شبکه فاضلاب شهری دسترسی ندارند، مورد استفاده قرار میگیرد. این سیستم به صورت مخزنی زیرزمینی در فاصله حدود 50 متر از ساختمان نصب میشود و نقش مهمی در جمعآوری، تصفیه و دفع فاضلاب ایفا میکند.
سپتیک تانک معمولاً از مواد مقاومی مانند پلاستیک، بتن یا فیبر شیشه ساخته میشود و به شکل استوانهای یا مستطیلی طراحی میشود. این سیستم از دو محفظه یا یک محفظه به همراه مخزن تشکیل میشود که فرآیند تصفیه فاضلاب را بهطور طبیعی انجام میدهد. فاضلاب وارد این تانک میشود و در آنجا با استفاده از فرآیندهایی چون تهنشینی، شناورسازی و تصفیه بیولوژیکی تصفیه میگردد.
بررسی تمامی اجزای سیستم سپتیک
اگر قصد خرید سپتیک فاضلاب را دارید، باید در مورد اجزای آن نیز اطلاعاتی داشته باشید. سیستم سپتیک فاضلاب خانگی از اجزای مختلفی تشکیل شده که هرکدام وظیفه خاصی دارند. این اجزاء شامل موارد زیر است:
- سیستم ورودی فاضلاب: این قسمت شامل لولهها و اتصالات است که فاضلاب خانگی را به مخزن وارد میکند. همچنین، بافل (میانگیر) ورودی از ورود لجن و مواد شناور به داخل مخزن جلوگیری میکند.
- مخزن اولیه سپتیک: این مخزن که 60 تا 70 درصد از حجم سیستم را به خود اختصاص میدهد، وظیفه تهنشین کردن مواد جامد و جدا کردن چربیها از فاضلاب را بر عهده دارد.
- دیوار جداکننده: این دیوار از ورود لجن و چربیهای شناور به مخزن تصفیه جلوگیری میکند.
- مخزن تصفیهکننده: این مخزن که تقریباً 30 درصد از حجم سیستم را شامل میشود، مواد تهنشینشده و شناور را در خود جمعآوری میکند.
- سیستم تهویه: گازهای تولید شده از فرآیندهای بیهوازی در این سیستم از مخزن خارج میشوند.
- سیستم خروجی: در این قسمت، پساب تصفیهشده از مخزن به لولهها و میدان تخلیه منتقل میشود.
بررسی دلایل خرید سپتیک فاضلاب
خرید و استفاده از سپتیک فاضلاب به عنوان یک سیستم تصفیه غیرمتمرکز برای مدیریت فاضلاب خانگی، مزایای بسیاری دارد که نه تنها به بهبود وضعیت بهداشتی و محیط زیستی کمک مینماید، بلکه از نظر اقتصادی هم مقرون به صرفه محسوب میشود. در ادامه به بررسی دلایل خرید این سیستم پرداخته میشود:
- مزایای سلامت عمومی: سیستم سپتیک فاضلاب با تصفیه صحیح فاضلاب، خطر انتقال بیماریها را از طریق آب آشامیدنی و آلودگیهای محیطی کاهش میدهد. این سیستم از ورود مواد بیماریزا به منابع آب جلوگیری کرده و به ارتقاء سلامت عمومی کمک میکند.
- مزایای زیستمحیطی: یکی از مهمترین دلایل استفاده از سپتیک فاضلاب، کاهش آلودگی محیط زیست است. این سیستم با تصفیه فاضلاب و جلوگیری از ورود آلایندهها به آبهای سطحی، به حفظ منابع آب و تغذیه سفرههای زیرزمینی کمک میکند.
- مزایای اقتصادی: سیستمهای فاضلاب غیرمتمرکز مانند سپتیک، در مقایسه با سیستمهای متمرکز هزینههای کمتری دارند. این سیستمها به جوامع کمک میکنند تا از هزینههای بالای ساخت تصفیهخانهها و شبکههای جمعآوری فاضلاب شهری بکاهند و مصرف انرژی را کاهش دهند.
- جلوگیری از آلودگی منابع آب: یکی دیگر از دلایل استفاده از سپتیک فاضلاب، جلوگیری از ورود مواد مضر به سفرههای آب زیرزمینی است. با استفاده از سپتیک، فاضلاب پیش تصفیه شده و به طور مستقیم به چاه یا سیستم فاضلاب شهری وارد نمیشود.
- پیش تصفیه بدون نیاز به انرژی یا اپراتور انسانی: سیستمهای سپتیک به گونهای طراحی شدهاند که بدون نیاز به اپراتور انسانی و مصرف انرژی، قادر به پیش تصفیه فاضلاب هستند.
- طول عمر بالا و هزینه کم نگهداری: سیستمهای سپتیک به دلیل طراحی ساده و ساختار محکم، طول عمر بالا و نیاز به نگهداری کم دارند. این ویژگی سبب میشود تا هزینههای بلندمدت کمتر شوند.
- قابلیت جابهجایی سیستم: یکی دیگر از ویژگیهای مفید سیستم سپتیک، امکان جابهجایی آن به منطقهای دیگر است.
چگونگی کارکرد سیستمهای سپتیک فاضلاب
سیستمهای سپتیک فاضلاب بهطور معمول با استفاده از مخزنی زیرزمینی که از بتن، فایبرگلاس یا پلیاتیلن ساخته میشود، فاضلاب را تصفیه میکنند. فاضلاب ابتدا از طریق لولههای ساختمان وارد این مخزن میشود. در مخزن، مواد جامد تهنشست شده و لجن تشکیل میدهند، در حالی که روغنها و مواد شناور دیگر بهعنوان زباله روی سطح آب جمع میشوند. این سیستم با استفاده از محفظهها و یک خروجی Tشکل، از ورود لجن به سمت منطقه تخلیه جلوگیری میکند و پساب مایع را به داخل میدان تخلیه منتقل میکند.
میدان تخلیه یک منطقه کمعمق و غنی از خاک غیر اشباع است که فاضلاب پیشتصفیه شده را از طریق لولههای متخلخل بهصورت فیلتر شده تخلیه میکند. در این مرحله، باکتریها و ویروسها بهطور طبیعی در خاک از بین میروند و مواد مغذی مضر نیز جذب میشوند. در نهایت، آب باقیمانده بهطور طبیعی به آبهای زیرزمینی نفوذ کرده و به بهبود کیفیت منابع آب کمک میکند.
معایب استفاده از سپتیک
استفاده از سیستمهای سپتیک فاضلاب میتواند معایبی نیز به همراه داشته باشد. یکی از مشکلات اصلی، احتمال ایجاد بوی بد در اطراف مخزن است که میتواند باعث آلودگی محیط و مزاحمت برای ساکنان شود. همچنین، در صورت عدم پیشتصفیه مناسب فاضلاب، ممکن است مخزن خراب شده و فاضلاب نشتی پیدا کند. پر شدن زودهنگام مخزن نیز یکی دیگر از مشکلات است که نیاز به تخلیه مداوم را به دنبال دارد، به ویژه زمانی که مواد جامد زیادی وارد سیستم شوند. علاوه بر این، سیستم سپتیک قادر به تصفیه کامل فاضلاب نیست و پساب و لجن تولید شده نیاز به تصفیه بیشتر یا تخلیه مناسب دارند.
انتهای پیام/